The Process Heat Status Quo
Natural Gas and Coal are the Default Fuels
Natural gas is the preferred fuel in many applications and regions because it is cheaper than oil, labor efficient, cheaper to transport in pipelines than coal, and burns cleaner than other fossil fuels. Many alternatives struggle to operate across a wide range of application sizes, while gas is flexible. Natural gas-fired boilers account for most steam production.
Coal sees a lot of use where gas is expensive, environmental restrictions are mild, and cheap labor is available. It is also great in high-temperature furnaces where its energy density and higher combustion temperature allow for a smaller furnace volume than natural gas.
Some regions might only have oil, electricity, or biomass for process heat. But these are exceptions, especially in the US. Many energy-intensive factories locate where energy prices are low and avoid these energy-poor places.
US natural gas is priced per 1000 standard cubic feet (MCF). I will list all contender pricing in dollars per MCF equivalent. The current spot price in the US is ~$4.50/MCF, but prices can vary wildly. Recent years have seen US prices as low as $1.50/MCF and European prices as high as $60/MCF. In less turbulent times, US prices are $3-$4/MCF, while Europe and Asia see $8-$12/MCF. Coal prices range from $2.50-$8/MCF, but the all-in price can vary wildly due to higher transportation, maintenance, and labor costs. Prices for natural gas and coal tend to track each other over lengthier periods due to fuel switching.
Why Steam is Valuable
Making steam for drying, distillation, etc., is one of the most common heat uses. Steam is the dominant process heat carrier because of water's ubiquity and properties. It works well for applications where temperature control is valuable because operators can finely control saturated steam temperature with pressure. The flow rate into steam jackets or heat exchangers is manageable because water releases healthy amounts of energy when it condenses. Volume shrinks dramatically after condensation, allowing new steam to flow in easily. It is much cheaper to pump liquid water/condensate back to the boiler than compress a gas.
The condensate leaving the steam jacket can be reheated in a gas-fired boiler or by excess heat from another part of the facility. Once it is steam again, it can go anywhere there are steam pipes. The use cases can be as small as steam tracing on piping to prevent freezing. Steam and condensate are very fungible, like energy currency within a plant.
Steam is best for low and medium-temperature heat because it is usually saturated, meaning the fluid temperature is at the boiling point. Water's boiling point increases as pressure increases, so higher temperatures bring higher pressures. Piping gets more expensive! Plants and factories sometimes use superheated steam, but water's heat transfer coefficient drops dramatically in the vapor phase, requiring much larger boilers to heat steam past saturation. And you can't control superheated steam's temperature with pressure as easily. There are often better options for high-temperature process heat.
Direct Heating
Some processes need a lot of heat at very high temperatures (1000+ Celcius). They might be less sensitive about maintaining a specific temperature or be so large that thermal mass moderates any swings. In these cases building a furnace directly into the process makes sense. Blast furnaces in integrated steel plants and kilns in cement manufacturing are classic cases. Coal has the dominant market share in these applications.
The Contenders
Geothermal
Pumping water down a deep geothermal well to make steam is an elegant solution. Transmission lines, interconnection agreements, and power plants are expensive, long lead time components for geothermal electricity projects that disappear when selling heat. Geothermal is at a massive disadvantage when it competes against gas to produce electricity because the average geothermal power plant is only ~11% efficient. New-age ones with hotter rock or supercritical CO2 turbines won't get much above 30%. Modern combined cycle natural gas power plants are 60% efficient. But geothermal is ~95% efficient in making steam, comparable to natural gas, and the well is the boiler!
Traditional hydrothermal geothermal resources are rarely in the same place as factories that need heat. Geothermal prospectors were stuck wasting most of their heat to make electricity to have a marketable product. But drilling deep wells in hot, dry granite unlocks "geothermal anywhere" and opens process heat sales to most industrial customers.
Deep wells in hot, dry rock are exciting because every foot deeper is more valuable. The higher rock temperature increases heat transfer and fluid return temperature. The properties of granite mean drilling costs may not increase exponentially, like in deep sedimentary basins. There is very little operating labor because it is just a hole in the ground with a pump circulating water. A pair of 20 km wells connected underground could produce steam at costs of $1/MCF equivalent - blowing away even American natural gas costs and making a mockery of European and Asian prices.
There have been a few positive updates since I last wrote about geothermal. First, the Utah FORGE project switched to a pure water drilling fluid with great results, proving the concept of water as a cheap, reliable high-temperature drilling fluid. Second, the elastomer mud motors used by the oil and gas industry have been improving rapidly. Over 70 rigs are drilling in the deep, hot Haynesville Shale. Operators want reliable downhole motors that can handle temperatures without accessories like mud coolers. Service companies have delivered, and now there is an off-the-shelf option that can get to 200+ Celsius if using mud coolers. About 1/3 of the Haynesville hasn't seen any drilling because it is hot enough to hurt bottom-hole assembly reliability, and shallower locations are still available. Evolutionary pressure will keep pushing motor and tool technology to open up this acreage over the coming years. And finally, startups and groups like Eavor and Utah FORGE continue to do enough drilling to justify the iteration of PDC bit designs suited for drilling in granite.
The upshot is there is no new technology needed to drill 10-12 km deep wells that can create steam for industries like pulp and paper, lumber, or food processing. The economics are still pretty marginal ($5-$8/MCF for a single, vertical wellbore), but they would improve rapidly if a startup could use Enhanced Geothermal Systems (EGS) or earn enough business to justify a contract for a rig capable of drilling deeper than 12 km. A new rig could also be designed for rail transportation to avoid the tyranny of oversize/overweight trucking costs. It is conceivable that <100 office staff managing 30-40 drilling rigs could replace 10% of total US gas demand in less than a decade. Each drilling rig would be like a 20-person carnival traveling from factory to factory on the railroad. Other technologies will struggle to beat a simple hole in the ground.
Electricity
Electricity to Heat
Process heat only comes from electricity in niche applications like electric arc furnaces because grid electricity is expensive. It is usually more economical to burn fossil fuels directly rather than suffer efficiency losses in generating and transporting electricity. Global industrial electricity prices range from $40/MWh to $200/MWh, the equivalent of $12/MCF to $60/MCF natural gas.
A better option could be hooking up solar panels or wind turbines directly to resistive heaters. Several startups want to store heat in objects like thermal bricks to allow 24/7 availability. They hope to compete in producing steam and direct heating (using brick-heated air).
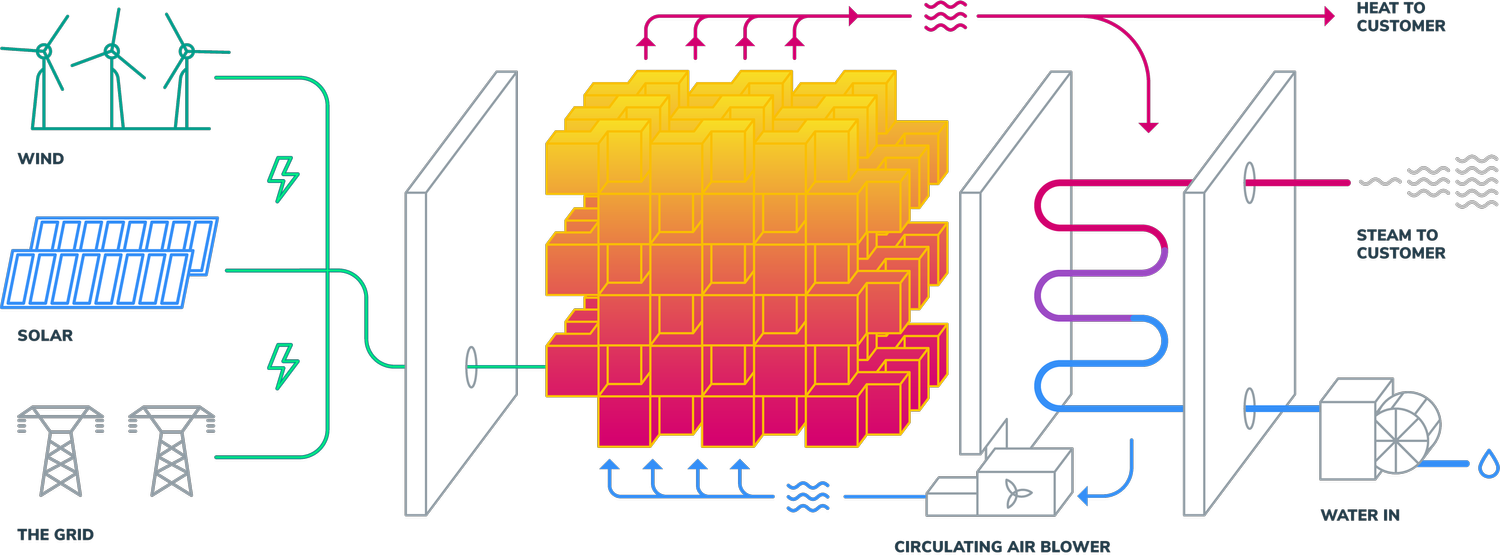
How to store electricity as heat; Source: Rondo.com
Onsite Solar/wind installations like this need fewer power electronics and other connections, saving money. A solar-oriented installation at today's prices (without subsidies) could deliver heat at an energy cost of ~$25/MWh or $7.30/MCF. I think solar power prices will keep falling, especially non-grid-tied applications. $10/MWh would be approaching $3/MCF plus CAPEX for the storage (An extra ~~$2-$3/MCF~~ $1/MCF). And in the US, the Inflation Reduction Act adds a $15/MWh subsidy, meaning solar is already near the $10/MWh price point.
Adapting Processes to Variable Electricity
A factory or plant could run when the sun shines or the wind blows with the proper design. The key is inexpensive CAPEX to make up for the low capacity factor. Most solutions will replace some classic high-temperature/high-pressure processes with electrochemistry instead. One possible example is producing iron in an electrolyzer and feeding it to steel minimills instead of processing the ore in a blast furnace. Electrochemistry is hard, so it is challenging to predict breakthroughs.
Substitution is another plausible option. Aluminum, sometimes known as "liquid electricity," could replace steel in many applications. Or concrete producers could use other binding agents besides cement.
Simply changing out coal-burning high-temperature furnaces with electric heating is challenging. First, these processes are too capital-intensive to run intermittently, requiring CAPEX reductions of >50% or a substantial business model change. Second, 24/7 electricity generators like nuclear or geothermal have trouble beating coal when utilities burn it inefficiently to produce electricity. Their costs would have to fall to $10/MWh to compete with directly burned coal. Even thermal storage of near-free renewables could struggle to beat coal in applications where it has a strong comparative advantage. The flip side is that many places in the world don't have cheap coal and could benefit from these technologies.
Heat Pumps
Carnot's Law governs heat pump efficiency, meaning they are less effective as the inlet and outlet temperatures get further apart. Traditional heating is more efficient past a limited temperature delta. There is some potential in providing low-grade heat, especially in small increments. Alternative options for bulk heat should be much cheaper.
Electricity to Fuel
Electricity, air, and water can become synthetic natural gas. But synthetic gas would be a premium product better suited for applications with variable demand like winter space heating, peak electricity generation, or rocket fuel.
The Electricity Summary
Electricity-to-heat will likely take some market share because it has low technical risk, can reach higher temperatures than other replacements, and is viable in small increments. Much of the world would happily pay $5-$10/MCF for high-quality industrial heat. Increasing market share will require new processes or advances in electrochemistry.
Hydrogen for Heat
Hydrogen is a derivative of fossil fuels or electricity manufactured by steam reforming or electrolysis. There is no existing hydrogen transportation infrastructure, so factories must manufacture it onsite. It is often simpler and cheaper to burn fossil fuels in stoichiometric amounts of oxygen to create a clean, easily capturable CO2 stream than steam reforming fossil fuels to produce hydrogen and capture CO2. Long-term hydrogen storage isn't helpful because most process heat applications have steady demand profiles. Thermal bricks can store enough heat and are cheaper in most scenarios.
The Inflation Reduction Act's hydrogen subsidy is so generous it could push hydrogen prices into negative territory. That generosity could lead to Congress amending the law, complicating decisions with multi-decade timelines. It is hard to know how much negative pricing and subsidies will drive adoption in process heat applications.
Nuclear
It is challenging for nuclear energy to compete in this space because process heat is low in value, most existing nuclear power plant technology cannot provide high temperatures, and fuel energy density only provides a slight advantage. Just the cost of light water reactor fuel would exceed deep geothermal's potential price point, and there are still the capital expenses of the reactor and heat exchangers. Non-light water nuclear plants can have higher temperatures than deep geothermal, but they are still low compared to electricity or fossil fuels. Labor and maintenance are significant factors for older designs.
Traditional light water reactors can produce affordable low and medium-temperature steam but only in massive quantities. NuScale's small modular reactor generates ~250 MW of heat, exceeding almost every user's needs. A cluster of plants might share a reactor and get $8-$9/MCF equivalent prices. The startup Last Energy has a more appropriate 60 MW of thermal output from its pressurized water reactor, and its cost aspirations put it around $5/MCF. The company hopes to have power plants in Poland within a few years. Time will tell if they can build reactors that meet their cost goals.
Designs similar to Westinghouse's eVinci microreactor could have long-term potential. It produces 15 MW of 600+ Celcius heat, which fits more applications. Control rods or drums would be the only moving parts, and its heat pipes allow for a small boiler. It ships in three containers vs. 70 for Last Energy, which is a ~5x smaller output-adjusted footprint. The fuel is fancy (TRISO), so it would need something cheaper. And other components like nuclear-grade graphite would need to fall dramatically in cost. $2-$3/MCF is possible in the most optimistic scenarios, but the early adopter price would be more like $10-$20/MCF.
Nuclear process heat hasn't made sense in the past because reactors were too large. Adoption depends on the development of cost-effective microreactors that can meet customer needs.
Summary
The status quo in process heat is difficult to beat in the US but much easier abroad. Incentive-boosted solar electricity is close to competitiveness and can win without subsidies in places that use fuel oil or have high natural gas and coal prices. Electricity will be the main competitor for fossil fuels in high-temperature applications, though it might require alternative processes. Geothermal has the lowest potential cost, but startups need to prove out deep drilling. Modularizing existing light water nuclear technology could be competitive for <300 C steam where energy prices are high, solar is expensive, and geothermal isn't mature. Advanced nuclear fission technologies still need work to reach cost parity. Subsidies may create some niches that wouldn't exist otherwise, but the market is too large for subsidies to overturn fundamentals set by physics and engineering. The process heat market is in the awkward stage where competitors are on the horizon, but deployment is minimal. Better drill bits and motors, cheaper solar panels, and new nuclear designs promise to reduce industrial heat costs while flattening geographical variation.
The Future of Industrial Process Heat
2023 January 5 Twitter Substack See all postsNew competitors hope to challenge fossil fuel's dominance.
The Process Heat Status Quo
Natural Gas and Coal are the Default Fuels
Natural gas is the preferred fuel in many applications and regions because it is cheaper than oil, labor efficient, cheaper to transport in pipelines than coal, and burns cleaner than other fossil fuels. Many alternatives struggle to operate across a wide range of application sizes, while gas is flexible. Natural gas-fired boilers account for most steam production.
Coal sees a lot of use where gas is expensive, environmental restrictions are mild, and cheap labor is available. It is also great in high-temperature furnaces where its energy density and higher combustion temperature allow for a smaller furnace volume than natural gas.
Some regions might only have oil, electricity, or biomass for process heat. But these are exceptions, especially in the US. Many energy-intensive factories locate where energy prices are low and avoid these energy-poor places.
US natural gas is priced per 1000 standard cubic feet (MCF). I will list all contender pricing in dollars per MCF equivalent. The current spot price in the US is ~$4.50/MCF, but prices can vary wildly. Recent years have seen US prices as low as $1.50/MCF and European prices as high as $60/MCF. In less turbulent times, US prices are $3-$4/MCF, while Europe and Asia see $8-$12/MCF. Coal prices range from $2.50-$8/MCF, but the all-in price can vary wildly due to higher transportation, maintenance, and labor costs. Prices for natural gas and coal tend to track each other over lengthier periods due to fuel switching.
Why Steam is Valuable
Making steam for drying, distillation, etc., is one of the most common heat uses. Steam is the dominant process heat carrier because of water's ubiquity and properties. It works well for applications where temperature control is valuable because operators can finely control saturated steam temperature with pressure. The flow rate into steam jackets or heat exchangers is manageable because water releases healthy amounts of energy when it condenses. Volume shrinks dramatically after condensation, allowing new steam to flow in easily. It is much cheaper to pump liquid water/condensate back to the boiler than compress a gas.
The condensate leaving the steam jacket can be reheated in a gas-fired boiler or by excess heat from another part of the facility. Once it is steam again, it can go anywhere there are steam pipes. The use cases can be as small as steam tracing on piping to prevent freezing. Steam and condensate are very fungible, like energy currency within a plant.
Steam is best for low and medium-temperature heat because it is usually saturated, meaning the fluid temperature is at the boiling point. Water's boiling point increases as pressure increases, so higher temperatures bring higher pressures. Piping gets more expensive! Plants and factories sometimes use superheated steam, but water's heat transfer coefficient drops dramatically in the vapor phase, requiring much larger boilers to heat steam past saturation. And you can't control superheated steam's temperature with pressure as easily. There are often better options for high-temperature process heat.
Direct Heating
Some processes need a lot of heat at very high temperatures (1000+ Celcius). They might be less sensitive about maintaining a specific temperature or be so large that thermal mass moderates any swings. In these cases building a furnace directly into the process makes sense. Blast furnaces in integrated steel plants and kilns in cement manufacturing are classic cases. Coal has the dominant market share in these applications.
The Contenders
Geothermal
Pumping water down a deep geothermal well to make steam is an elegant solution. Transmission lines, interconnection agreements, and power plants are expensive, long lead time components for geothermal electricity projects that disappear when selling heat. Geothermal is at a massive disadvantage when it competes against gas to produce electricity because the average geothermal power plant is only ~11% efficient. New-age ones with hotter rock or supercritical CO2 turbines won't get much above 30%. Modern combined cycle natural gas power plants are 60% efficient. But geothermal is ~95% efficient in making steam, comparable to natural gas, and the well is the boiler!
Traditional hydrothermal geothermal resources are rarely in the same place as factories that need heat. Geothermal prospectors were stuck wasting most of their heat to make electricity to have a marketable product. But drilling deep wells in hot, dry granite unlocks "geothermal anywhere" and opens process heat sales to most industrial customers.
Deep wells in hot, dry rock are exciting because every foot deeper is more valuable. The higher rock temperature increases heat transfer and fluid return temperature. The properties of granite mean drilling costs may not increase exponentially, like in deep sedimentary basins. There is very little operating labor because it is just a hole in the ground with a pump circulating water. A pair of 20 km wells connected underground could produce steam at costs of $1/MCF equivalent - blowing away even American natural gas costs and making a mockery of European and Asian prices.
There have been a few positive updates since I last wrote about geothermal. First, the Utah FORGE project switched to a pure water drilling fluid with great results, proving the concept of water as a cheap, reliable high-temperature drilling fluid. Second, the elastomer mud motors used by the oil and gas industry have been improving rapidly. Over 70 rigs are drilling in the deep, hot Haynesville Shale. Operators want reliable downhole motors that can handle temperatures without accessories like mud coolers. Service companies have delivered, and now there is an off-the-shelf option that can get to 200+ Celsius if using mud coolers. About 1/3 of the Haynesville hasn't seen any drilling because it is hot enough to hurt bottom-hole assembly reliability, and shallower locations are still available. Evolutionary pressure will keep pushing motor and tool technology to open up this acreage over the coming years. And finally, startups and groups like Eavor and Utah FORGE continue to do enough drilling to justify the iteration of PDC bit designs suited for drilling in granite.
The upshot is there is no new technology needed to drill 10-12 km deep wells that can create steam for industries like pulp and paper, lumber, or food processing. The economics are still pretty marginal ($5-$8/MCF for a single, vertical wellbore), but they would improve rapidly if a startup could use Enhanced Geothermal Systems (EGS) or earn enough business to justify a contract for a rig capable of drilling deeper than 12 km. A new rig could also be designed for rail transportation to avoid the tyranny of oversize/overweight trucking costs. It is conceivable that <100 office staff managing 30-40 drilling rigs could replace 10% of total US gas demand in less than a decade. Each drilling rig would be like a 20-person carnival traveling from factory to factory on the railroad. Other technologies will struggle to beat a simple hole in the ground.
Electricity
Electricity to Heat
Process heat only comes from electricity in niche applications like electric arc furnaces because grid electricity is expensive. It is usually more economical to burn fossil fuels directly rather than suffer efficiency losses in generating and transporting electricity. Global industrial electricity prices range from $40/MWh to $200/MWh, the equivalent of $12/MCF to $60/MCF natural gas.
A better option could be hooking up solar panels or wind turbines directly to resistive heaters. Several startups want to store heat in objects like thermal bricks to allow 24/7 availability. They hope to compete in producing steam and direct heating (using brick-heated air).
How to store electricity as heat; Source: Rondo.com
Onsite Solar/wind installations like this need fewer power electronics and other connections, saving money. A solar-oriented installation at today's prices (without subsidies) could deliver heat at an energy cost of ~$25/MWh or $7.30/MCF. I think solar power prices will keep falling, especially non-grid-tied applications. $10/MWh would be approaching $3/MCF plus CAPEX for the storage (An extra ~~$2-$3/MCF~~ $1/MCF). And in the US, the Inflation Reduction Act adds a $15/MWh subsidy, meaning solar is already near the $10/MWh price point.
Adapting Processes to Variable Electricity
A factory or plant could run when the sun shines or the wind blows with the proper design. The key is inexpensive CAPEX to make up for the low capacity factor. Most solutions will replace some classic high-temperature/high-pressure processes with electrochemistry instead. One possible example is producing iron in an electrolyzer and feeding it to steel minimills instead of processing the ore in a blast furnace. Electrochemistry is hard, so it is challenging to predict breakthroughs.
Substitution is another plausible option. Aluminum, sometimes known as "liquid electricity," could replace steel in many applications. Or concrete producers could use other binding agents besides cement.
Simply changing out coal-burning high-temperature furnaces with electric heating is challenging. First, these processes are too capital-intensive to run intermittently, requiring CAPEX reductions of >50% or a substantial business model change. Second, 24/7 electricity generators like nuclear or geothermal have trouble beating coal when utilities burn it inefficiently to produce electricity. Their costs would have to fall to $10/MWh to compete with directly burned coal. Even thermal storage of near-free renewables could struggle to beat coal in applications where it has a strong comparative advantage. The flip side is that many places in the world don't have cheap coal and could benefit from these technologies.
Heat Pumps
Carnot's Law governs heat pump efficiency, meaning they are less effective as the inlet and outlet temperatures get further apart. Traditional heating is more efficient past a limited temperature delta. There is some potential in providing low-grade heat, especially in small increments. Alternative options for bulk heat should be much cheaper.
Electricity to Fuel
Electricity, air, and water can become synthetic natural gas. But synthetic gas would be a premium product better suited for applications with variable demand like winter space heating, peak electricity generation, or rocket fuel.
The Electricity Summary
Electricity-to-heat will likely take some market share because it has low technical risk, can reach higher temperatures than other replacements, and is viable in small increments. Much of the world would happily pay $5-$10/MCF for high-quality industrial heat. Increasing market share will require new processes or advances in electrochemistry.
Hydrogen for Heat
Hydrogen is a derivative of fossil fuels or electricity manufactured by steam reforming or electrolysis. There is no existing hydrogen transportation infrastructure, so factories must manufacture it onsite. It is often simpler and cheaper to burn fossil fuels in stoichiometric amounts of oxygen to create a clean, easily capturable CO2 stream than steam reforming fossil fuels to produce hydrogen and capture CO2. Long-term hydrogen storage isn't helpful because most process heat applications have steady demand profiles. Thermal bricks can store enough heat and are cheaper in most scenarios.
The Inflation Reduction Act's hydrogen subsidy is so generous it could push hydrogen prices into negative territory. That generosity could lead to Congress amending the law, complicating decisions with multi-decade timelines. It is hard to know how much negative pricing and subsidies will drive adoption in process heat applications.
Nuclear
It is challenging for nuclear energy to compete in this space because process heat is low in value, most existing nuclear power plant technology cannot provide high temperatures, and fuel energy density only provides a slight advantage. Just the cost of light water reactor fuel would exceed deep geothermal's potential price point, and there are still the capital expenses of the reactor and heat exchangers. Non-light water nuclear plants can have higher temperatures than deep geothermal, but they are still low compared to electricity or fossil fuels. Labor and maintenance are significant factors for older designs.
Traditional light water reactors can produce affordable low and medium-temperature steam but only in massive quantities. NuScale's small modular reactor generates ~250 MW of heat, exceeding almost every user's needs. A cluster of plants might share a reactor and get $8-$9/MCF equivalent prices. The startup Last Energy has a more appropriate 60 MW of thermal output from its pressurized water reactor, and its cost aspirations put it around $5/MCF. The company hopes to have power plants in Poland within a few years. Time will tell if they can build reactors that meet their cost goals.
Designs similar to Westinghouse's eVinci microreactor could have long-term potential. It produces 15 MW of 600+ Celcius heat, which fits more applications. Control rods or drums would be the only moving parts, and its heat pipes allow for a small boiler. It ships in three containers vs. 70 for Last Energy, which is a ~5x smaller output-adjusted footprint. The fuel is fancy (TRISO), so it would need something cheaper. And other components like nuclear-grade graphite would need to fall dramatically in cost. $2-$3/MCF is possible in the most optimistic scenarios, but the early adopter price would be more like $10-$20/MCF.
Nuclear process heat hasn't made sense in the past because reactors were too large. Adoption depends on the development of cost-effective microreactors that can meet customer needs.
Summary
The status quo in process heat is difficult to beat in the US but much easier abroad. Incentive-boosted solar electricity is close to competitiveness and can win without subsidies in places that use fuel oil or have high natural gas and coal prices. Electricity will be the main competitor for fossil fuels in high-temperature applications, though it might require alternative processes. Geothermal has the lowest potential cost, but startups need to prove out deep drilling. Modularizing existing light water nuclear technology could be competitive for <300 C steam where energy prices are high, solar is expensive, and geothermal isn't mature. Advanced nuclear fission technologies still need work to reach cost parity. Subsidies may create some niches that wouldn't exist otherwise, but the market is too large for subsidies to overturn fundamentals set by physics and engineering. The process heat market is in the awkward stage where competitors are on the horizon, but deployment is minimal. Better drill bits and motors, cheaper solar panels, and new nuclear designs promise to reduce industrial heat costs while flattening geographical variation.