Nuclear's Dark Period
Accidents and Poor Reliability Ding Nuclear
Safety concerns increased after events at Brown's Ferry (1975), Rancho Seco (1978), and Three Mile Island (1979). These events generated a long list of deterministic rules, most of which are still in the books. Construction times for already under construction plants increased. Three Mile Island usually takes the blame, but analysis shows only about 12% of retrofit costs were from changes specific to that incident. The combination of utilities spending more to improve reliability and changes from the other events in the late 1970s make up the balance.
Safety controls increased the difficulty of building new power plants and required upgrades at existing power plants. The average capacity factor was around 60% throughout the 1970s and 1980s. Nuclear power plants were more expensive while also being unreliable.
Competitors Get Unleashed
The government hamstrung nuclear's competitors in the 1960s and 1970s. Natural gas was heavily regulated, with new gas power plants de facto banned for some time. Coal is cheap at the mine but expensive to move, requiring barge or rail to keep prices reasonable. Regulated railroads were pricey.
The early 1980s saw the deregulation of both natural gas and railroads. Natural gas replaced underperforming power plants like Rancho Seco. Cheaper rail costs made existing coal plants cheaper to run and mitigated the pain of new laws to reduce sulfur dioxide emissions. Many utilities found they could ditch local, high-sulfur coal and buy low-sulfur coal from the Powder River Basin in Wyoming. Prices in a sulfur dioxide cap and trade scheme ended up being a fraction of the expected cost.
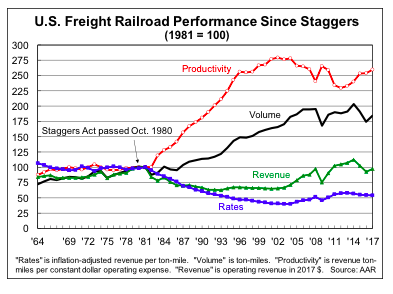
Source: sbecouncil.org
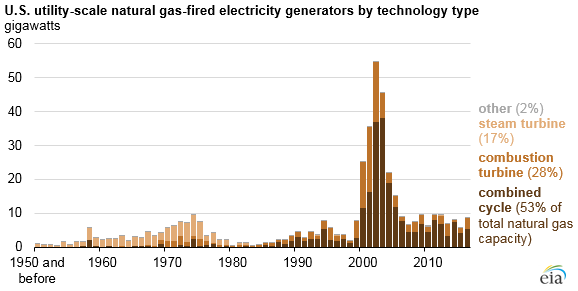
Source: EIA
Nuclear power's competitors rapidly improved their position in the market.
Demand Slows
Electricity growth was in the high single digits going into the 1970s, forcing utilities to build power plants like crazy. Demand growth slowed for reasons like efficiency boosting laws.
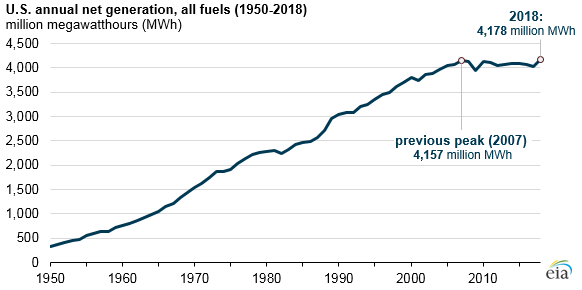
Source: EIA
The need for new power plants declined.
Increasing Output Delayed Need for New Power Plants
From the 1980s to today, the capacity factor of US nuclear power plants increased from <60% to >90%. The improved capacity factor meant that utilities got one free power plant for every two existing ones. Many of the expansion plans called for new reactors at existing facilities. The increased output removed the need for new reactors.
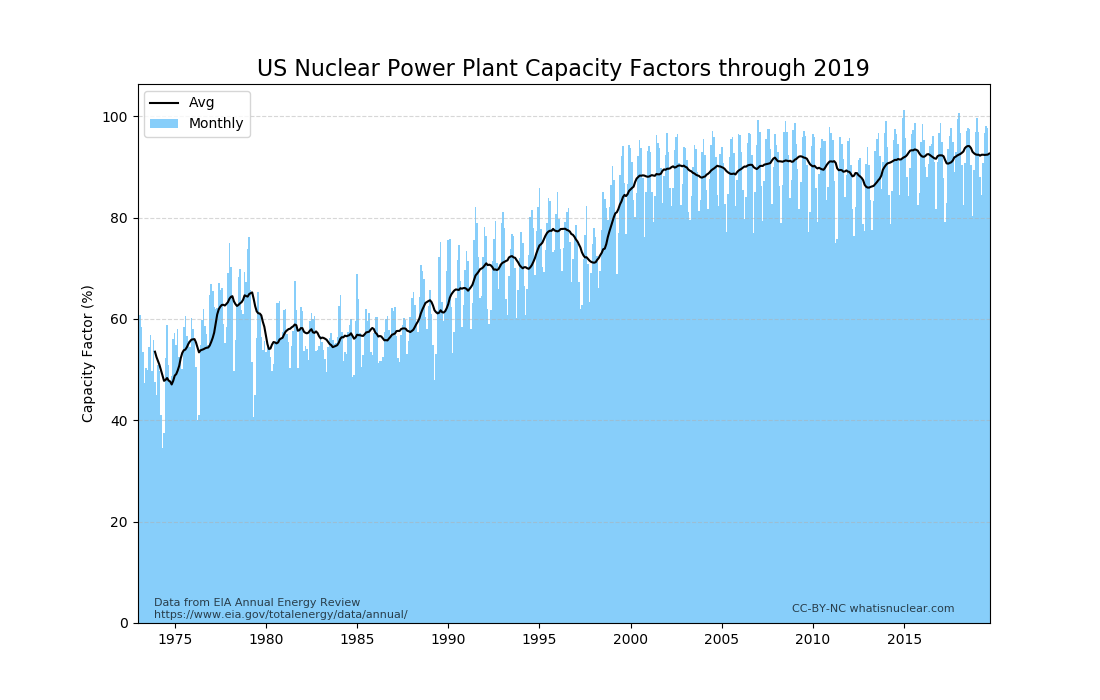
Source: Whatisnuclear.com
The story of how the industry did this involves better-managed utilities, a strong effort from the industry group (INPO), and regulation changes.
The Nuclear Industry's Turnaround
Institute of Nuclear Power Operations
The nuclear industry funds the Institute of Nuclear Power Operations (INPO) to promote safety and reliability. INPO started in 1979 following the Three Mile Island accident. It conducts regular inspections at all nuclear power plants, and many INPO employees are "on loan" from the utilities. It rates plant performance based on inspections and shares findings and best practices with all members, but not the public. INPO holds its members to a standard of excellence, going much further than the NRC, which only manages safety standards.
It may seem strange to have an organization like this, especially in the United States. But the nuclear industry was 100% regulated utilities with territorial monopolies in 1979. There are only a few designs, so sharing information has great benefits with no competition downsides. Utilities take INPO very seriously and often loan their best employees for tours of duty there.
INPO recognized right away that well-run plants are both safe and reliable. Human factors and organizational culture are points of intense focus. Accidents or poor economics could end the industry. Accidents are a more immediate threat because regulated monopolies own most nuclear power plants, and politicians are willing to dole out subsidies. Preventing accidents requires constant vigilance; one laggard could ruin the entire industry. There is a symbolic carving of "Excellence" in front of INPO's headquarters, with the "E" unfinished.
Another benefit of INPO is to create a powerful interest group to counter anti-nuclear groups like the "Union of Concerned Scientists" lobbying the NRC. In some cases, like worker training standards, NRC declined to create rules as long as utilities followed INPO's recommendations. INPO also sends its inspection data to the NRC.
In a 1985 update, we see that the industry was already achieving cultural and operational improvements in many areas:
- Significant events per unit declined from 1.64 in 1981 to 0.53 in 1985.
- Unplanned automatic scrams (reactor shutdowns) decreased from 6 per unit-year to 3.5 between 1980 and 1984.
- Radiation exposure for boiling water reactor employees fell from 1230 man-rem per unit-year to 896 while falling from 597 to 394 in pressurized water reactors.
- Lost time accidents fell from 2.14 per 200,000 man-hours to 0.64.
Plant capacity factors are a lagging indicator and would begin a long climb in the late 1980s. One paradigm exemplifies the changes in the nuclear industry brought by utilities and INPO: Probabilistic Risk Assessments.
How Probabilistic Risk Assessments Change the Game
Probabilistic risk assessments (PRAs) emerged in 1975 and increased in prominence until full adoption in 1995. These assessments utilize a fault tree approach. They model a triggering event and calculate the probability that each safety feature will succeed in preventing core damage, a release to the environment, and an impact on the public. The standard for preventing core damage is one event in 10,000 reactor years and one in 100,000 reactor years for a release. The US currently has 93 reactors running, so we expect a core damage event every 107 years and a release every 1070 years. In practice, most plants exceed this margin by a factor of two.
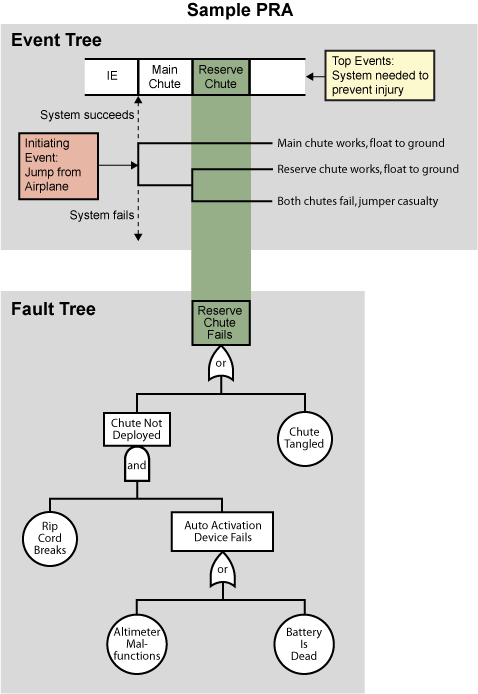
How PRAs work. Source: NRC
The nuclear industry's adoption of PRAs changed the mindset of how to operate the plants. There was a rigid hierarchy of "safety equipment" and "non-safety equipment." The mentality inevitably led to a focus on safety equipment at the expense of plant reliability. Once operators started using PRAs, they discovered that many "non-safety" pieces of equipment were safety barriers and that the safest way to run a plant is at design conditions. Startups and shutdowns are often the highest risk periods for any industrial facility, nuclear power plants included.
PRAs better aligned operating costs and safety for the industry. Better reliability lowers costs for mostly fixed-cost nuclear power plants.
A pathway for increasing plant reliability was doing much more maintenance while the plant was online. The PRAs give utilities a guide on what equipment can be taken offline for repair or preventive maintenance on any day without increasing risk above the threshold. It avoids scenarios where you might accidentally take several barriers offline at once.
Time offline for fueling and repairs also decreased dramatically. There was less maintenance during planned outages, and the industry improved outage planning to complete tasks faster.
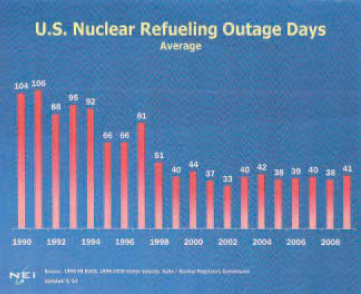
Source
One story shows the complexity of nuclear engineering and the change the PRA mindset brought. Stellite is a metal alloy that is great for making parts of valves like seats. But Stellite contains cobalt which can form Cobalt-60 when hit with neutrons. Cobalt-60 releases very high-energy gamma rays that can harm workers. Fluid can erode parts of the valve while flowing past. Those particles go through the reactor, get hit with neutrons, then settle down into parts of the systems like traps. When workers clean these areas, they can get exposed to high-energy radiation. The original directive from regulators was to ban using Stellite in equipment with possible exposure to neutrons. Plants had to use valves that required more maintenance and were more likely to leak. Risk calculations uncovered that worker exposure would be lower while using Stellite under some scenarios because of reduced maintenance and testing. The cost goes down while safety and reliability increase.
Interaction with Traditional Rules and PRAs
Many of the deterministic rules still exist. Everyone has to follow the rules, but PRAs are like a relief valve. For instance, there is a rule that safety-related equipment cannot be out of service for over 72 hours, or the plant must shut down. But there is often equipment that is hard to access and service. Repair in under 72 hours isn't physically possible. The utility can ask for an exception from the NRC. Keeping the plant online is likely safer if the utility can fix it in a reasonable amount of time. The PRA process provides evidence that allows the exception.
Following the full adoption of PRAs in 1995, NRC now provides performance-based alternatives for any new rule and often adds them to old regulations if desired by utilities. The switch to performance from deterministic rules isn't always easy or a low-cost option. NFPA 805 is an effort that started in the mid-2000s to move fire protection from deterministic to risk-informed, performance-based regulation. It is to be followed by similar conversions to seismic and flooding risks. A conference between the utilities and NRC about early implementation is illuminating. The early plants to pilot the process, like Oconee and Harris, saw costs much higher than meeting deterministic rules. Since fires can start in many places, the PRAs had thousands of initiating events to analyze. Completing the work took ~50,000 hours per plant. Part of the cost problem was that some initial variables for calculating risk were too conservative by a factor of 10. The utilities responded by requesting many exceptions and providing alternatives that led to lots of back and forth between the utilities and NRC, using many engineering hours. Both sides agreed to changes to try to make it easier for the rest of the nuclear fleet to switch.
Light Water Reactors are Labor Intensive
Light water reactors have hundreds of engineering subsystems. One way to think about their design is that they use simple parts but have a complex overall architecture. A multi-billion dollar chemical complex might have less than ten non-management engineers. A light water nuclear power plant needs hundreds. Even without regulation, the power plants still require many of these engineers. An engineer at a refinery doesn't have to worry about his isotopes changing! That simplifies a lot of work. A carbon steel pipe with oil in it might last hundreds of years. Piping and equipment exposed to neutrons, radiation, or hydrogen and oxygen from electrolysis in the reactor need more maintenance and care. It takes a lot of workers to complete the required maintenance safely.
The regulation does add work. It takes a lot of engineering resources to complete PRAs. And having PRAs requires competent engineers and scientists to work for the NRC.
Less regulation and better regulation would certainly reduce costs, but the impact on operating costs for existing plants is less than we'd hope. Many plants in deregulated markets will still struggle when electricity prices are low from cheap gas or renewables, especially when they face repair bills like replacing steam generators.
Is ALARA Making Nuclear Power More Expensive?
The nuclear industry aims to keep radiation exposure As Low As is Reasonably Achievable (ALARA). ALARA is an example among critics of how the government won't ever let nuclear be cheap. But would things change if ALARA went away?
First, anyone that has worked in a nuclear power plant or a large chemical processing facility knows how specialized these workers are. At the chemical plant where I worked, the average employee tenure was around 18 years. The norm is to work your entire life at one facility. There are few others like it, and the pay is higher due to the quality of employees required and the skills and experience you develop. The workforce is unionized, or owners fear unionization.
Another thing that becomes apparent is that these facilities' complexity and maintenance requirements require an extremely high-performance culture. The expectation is that the plant always runs and only bad things can happen. For owners, many deviations have extreme tail risks where workers die; or the population outside the plant gates sees impacts.
You can't expect employees to participate in this culture if you don't value their health and lives. Just like the business expectation is that there will be continuous improvement in plant operations (nothing is ever good enough), the only acceptable long-term goal for safety and health is zero impact.
Furthermore, accidents are non-linear. People can die falling from twelve inches. If you want zero workplace deaths, you have to eliminate all falls. Radiation exposure also has non-linearities. A safe exposure outside your body might not be safe if you accidentally stick your pen in your mouth while filling out paperwork. Other factors can compound so that an employee that makes a mistake and exposes themselves to radiation with a large effective dose. Like with falls, the best way to prevent the risk of harm is to push exposure risk as low as possible. It is unreasonable to compare the risk to a job like a flight attendant because their radiation exposure does not have the same non-linearity.
The reality on the ground is that nuclear organizations are committed to ALARA from top to bottom, and they would be regardless of regulation. As an antidote, you can read the famous business case study of how Alcoa turned its business around by focusing on safety.
Summarizing Nuclear's Progress
The industry took unreliable plants with unacceptable safety and turned them into the safe, reliable plants we know today. Collaboration between utilities, INPO, and NRC to create performance-based alternatives was important. But these changes aren't a silver bullet.
What does this experience tell us about building new reactors?
Lessons For Future Reactors
Many people are upset that we have built more paper reactors than real ones in recent decades. They blame the NRC licensing process and ALARA while assuming that the economics would work themselves out without regulation. There is no avoiding the details of nuclear engineering to find something closer to the truth. I'll walk you through the tradeoffs nuclear engineers face and the resulting design choices.
I'm going to accept that future reactors will go through probabilistic risk analysis. So complicated designs will be harder to build, more expensive to maintain, and more challenging to license. A safe, complex design is just as costly to license as an unsafe, complex design. And an extremely safe and simple design might be cheap to license in comparison. PRA cost and effort are related to complexity, not safety.
It's All About the Neutrons
Fission is when an atom splits into two smaller atoms, often releasing neutrons and other radiation. Only certain isotopes are fissile. They naturally undergo fission slowly but seldom have fission chain reactions like atom bombs or nuclear power plants. Uranium-235 (U235) is the most common fuel because we can mine it easily.
To create a chain reaction, the neutrons from a splitting atom must hit other atoms causing them to split and release more neutrons. Engineers consider how likely a neutron collision with another fissile atom is when designing nuclear fuel. There need to be enough atoms in a small space. Each fissile element has a minimum mass required to sustain a chain reaction (depending on conditions). The speed of neutrons is a chief consideration. Atoms have different "cross-sections," where they are more likely to collide with neutrons at certain speeds than others. Non-fissile atoms turn into a different isotope when they capture a neutron instead of splitting.
U235 is much more likely to capture slow neutrons but produces fast neutrons when it splits. Most existing nuclear reactors use a moderator to slow neutrons down, reducing the amount of uranium needed to start a reaction by increasing the chance of collisions. Hydrogen is the best moderator because it has the same mass as neutrons and absorbs more kinetic energy than larger atoms. Conveniently, there are a lot of hydrogen atoms in water molecules, and most reactors use water as a moderator. Graphite is the next most popular choice.
Good moderators also need to avoid capturing neutrons. Captured neutrons can't participate in a chain reaction and usually make whatever is capturing them radioactive. "Light" water is a mediocre moderator because its hydrogen atoms can capture neutrons and become deuterium. Heavy water reactors use only deuterated water to improve performance by reducing moderator capture of neutrons.
Some reactor designs have no moderator and are known as fast reactors. They can use fuel more efficiently because some fissile isotopes created by neutron bombardment only capture fast neutrons. Moderated reactors leave these isotopes in their spent fuel, and the isotopes can stay radioactive for hundreds of thousands of years. Fast reactor waste is often safe after a few hundred years. Because the main fissile isotope (U235) is less likely to capture fast neutrons, fast reactors need more starting fuel, among other complications.
A central tension in nuclear engineering is that the fluid heated near the reactor has very different requirements than the fluid that powers the heat engine. Most designs have a reactor loop and a power generation loop, while other thermal power plants only have a power generation loop. The neutrons are why many concepts have helium, sodium, molten salt, or lead in the reactor loop.
Control rods contain materials that capture neutrons easily, like boron. Removing the rod increases neutrons available to sustain chain reactions.
The Logic of Water Moderated Reactors
Using water as a moderator has many advantages. It has a low freezing point, is well understood, pumps readily, and is an excellent heat transfer fluid.
The limitations are that it has a low boiling point and becomes radioactive in a reactor. The low boiling point requires pressurized water reactors (PWRs) and boiling water reactors (BWRs) to use high pressure to reach a reasonable temperature and heat engine efficiency. Light water reactors must also use enriched fuel to overcome water's neutron absorption that stymies chain reactions. Their fuel is typically 3%-5% U235 vs. 0.7% for natural uranium.
Heavy water-moderated reactors (HWRs) like Canada's CANDU are strange beasts. They can use natural uranium since heavy water is an excellent moderator. They also don't require a reactor pressure vessel. The fuel and coolant are in pipes submerged in heavy water. Theoretically, you could use a gas or organic coolant, but CANDU doesn't. It runs like a pressurized water reactor with water coolant and a steam generator where the coolant heats a clean water loop. HWRs require a much larger reactor, and heavy water is expensive. Canada has lots of uranium, no nuclear weapons program to share enrichment facilities/expertise, and struggled to build large pressure vessels during reactor development. CANDU fits within those requirements.
Again, water-moderated reactors have many parts and a deceiving amount of complexity. But the components are pumps, valves, machined parts, water-water heat exchangers, and turbines that are relatively straightforward compared to non-water coolant designs.
The Rise of Passive Safety in Gen III and Gen IV Reactors
Reactor safety took center stage after accidents like Three Mile Island and Chernobyl. The most popular concept is to use passive safety systems instead of active ones. Passive safety means making changes like using the natural circulation of coolant to cool the reactor instead of pumps. These changes can make the reactors a few orders of magnitude safer while decreasing part count.
The negative is that the plants require more upfront engineering and much tighter construction tolerances than Gen I and II designs. Disaster can strike when attempting to build such facilities with regular construction practices like incomplete detailed drawings at the start of construction (cough, VC Summer, cough). Passive safety reactors don't necessarily have fewer initiating events in PRAs, and models need more precision to complete the trees adequately. Complexities around radioactive fluid, heat from radioactive decay of fuel, and damage from external events still need modeling.
It may seem counterintuitive that these plants are harder to build with fewer parts, but passive systems are more sensitive to changes than active systems. Small changes in piping can change the natural circulation rate. An engineer can complete the basic design for an active cooling loop on a few sheets of paper. Moving piping during construction is no big deal because the engineer undoubtedly oversized the pumps to handle small increases in pressure drop. That probably happened in the field, on the fly, for early reactors. Modeling natural circulation in complex piping requires a computer simulation, and you'd have to rerun the entire model to check if the circulation rate remains acceptable after any change. Passive safety systems can tightly couple subsystem design.
A large Gen-III facility requires unprecedented detail for one of the most complex construction projects humans have ever undertaken. The decision to use some modular components for the AP1000 only exacerbated the challenge. It is funny that Westinghouse and CBI needed more detailed engineering to succeed than NRC required for licensing.
Once we consider the complexity paired with the loose coupling of older designs, it starts to make sense how some plants in the 1960s looked so inexpensive to build. They had lower-paid workers building labor-intensive designs that were tolerant of construction errors, while lacking many safety and reliability features that facility owners retrofitted later. And construction companies built the lowest-price plants on fixed-price contracts where they took a bath due to cost overruns. You couldn't repeat that today due to labor costs alone. And as a sanity check, we see that today's vastly simpler gas power plants cost more than some of the claimed 1960s prices you see in papers like Lovering et al.
Light Water Small Modular Reactors
These issues led to the desire for smaller reactors built in factories, known as Small Modular Reactors (SMRs). SMRs typically range from ~50 megawatt to ~300 megawatt. The idea is that the extra engineering will be spread over many identical units while factory construction can better accommodate tighter tolerances.
They lose scale in items like vessels, pumps, turbines, and heat exchangers but gain factory efficiency. No one expects these designs to set records for low-price electricity, but they do have orders in places where electricity is expensive.
The NRC recently (2022) approved the first light water SMR design from the startup NuScale.
Advanced Non-Light Water Reactors
It wasn't clear which designs would be the best early in the nuclear era. There was lots of experimentation, and we built gas-cooled reactors, metal-cooled fast reactors, etc. All of the light water reactor alternatives proved to be uneconomic. When the industry started modernizing regulations, every commercial reactor operating was a light water reactor. And those are the only regulatory codes that were updated. Once SMRs appeared on the horizon, the NRC focused on modernizing regulations for light water small modular reactors, like NuScale.
Then startups came out of the woodwork wanting to build non-light water reactors. So the slow machinery of bureaucracy has started on programs to modernize codes for these reactors. The most logical reasons for the re-emergence of these designs have been falling wholesale electricity prices or a desire to utilize fast reactor fuel cycle advantages. Some non-light water reactors can have a fraction of the subsystems as a light water reactor and better efficiency but are more technologically challenging and expensive to maintain. The startups hope they can overcome the technical and economic challenges to better compete in competitive electricity markets.
Sodium-Cooled Fast Reactors
Fast reactors using a liquid coolant have two popular options, one being sodium. Like moderated reactors, the coolant shouldn't capture neutrons. But the atom also needs to be relatively big, so neutrons bounce right off and maintain speed. Compact fast reactor cores need fluids with exceptional heat transfer. Sodium fits the bill and has a high boiling point, allowing the reactor to reach higher temperatures at atmospheric pressure.
The downsides are rough. Sodium catches on fire when exposed to air and violently explodes in contact with water. The freezing point is high, so care has to be taken to keep it from freezing in pipes, pumps, and valves. Natural circulation of the coolant in pools is a feature of almost all designs to improve safety and reduce the risk of freezing in equipment.
One of the first US nuclear submarines tested a sodium-cooled reactor. Admiral Rickover had this to say:
In Rickover's words they were "expensive to build, complex to operate, susceptible to prolonged shutdown as a result of even minor malfunctions, and difficult and time-consuming to repair."
The admiral had it ripped out and replaced with a light water reactor.
The BN-600 is a long-running, commercial sodium-cooled reactor in Russia. It suffered a few dozen fires early in its life but hasn't had one in decades. The plant's lifetime capacity factor is ~75%, but its recent performance is in the high 80s. Lengthy fueling outages prevent capacity factor from increasing much more. Russia recently completed the BN-800. The motivation is to use a "closed-fuel cycle" (mixed uranium and plutonium) and burn weapons-grade plutonium.
Success is possible, especially with pool-style designs, but complexity and cost are still high. The power plants took over a decade to build and have three fluid loops, a sodium pool around the reactor and a second sodium loop that transfers heat from the reactor pool to a steam generator.
GE is designing a conventional sodium-cooled fast reactor similar to the BN-600 and the Experimental Breeder Reactor II.
TerraPower is a US startup working on a 345 megawatt sodium-cooled fast reactor. They also want to attach molten salt storage to the facility to allow the plant to deliver more power at peak times. Combining two challenging technologies like that is pretty absurd. But they recently raised another $750 million, so some disagree with my assertion.
Oklo is designing a 1.5 megawatt sodium-cooled fast reactor with a supercritical CO2 power cycle. Using CO2 working fluid in a closed Brayton cycle can improve efficiency and cost over steam turbines. It also eliminates the potential for water contact. Oklo could build larger power plants based on the design if successful.
The NRC canceled Oklo's application after the NRC was unhappy with their progress (while still allowing them to reapply later). It's clear that Oklo didn't provide the detailed engineering NRC requires in its licensing activities. Oklo also chose a strange licensing route. They avoided the process that NRC is working on to modernize licensing for non-LWRs and submitted alternative risk calculation methods. The NRC asked them to show their work, and Oklo did not provide the details to the NRC's satisfaction about topics like "maximum credible accident size." As we've seen before, performance-based is an option. But it can be engineering intensive when dealing with complex reactor configurations like sodium-cooled fast reactors and mostly unproven power cycles like a CO2 Brayton cycle.
The appeal of sodium-cooled fast reactors is they are the only fast reactors with a long operating history. That makes them a natural choice for deploying fast reactors that can utilize waste from light water reactors. But they are still challenging to build and prototype. And they aren't likely to set cost records.
Lead-Cooled Fast Reactors
Lead is the other main option for fast reactors using liquid coolant. It is poisonous, but at least it doesn't catch on fire! Reduction of fire risk could allow the power loop heat exchanger to be in the lead pool, eliminating an extra fluid loop that traditional sodium-cooled reactors require to keep water away from the reactor. It has similar drawbacks with a high freezing point, and its heat transfer properties aren't as good as sodium. Corrosion is a concern, as well. Like sodium, pool-style designs are popular.
The Soviet Alpha-Class submarines used lead-cooled fast reactors. Russia has plans to build several commercial plants using the technology. Westinghouse has a lead-cooled concept, but interest seems to be more lukewarm in the West.
Gas-Cooled Fast Reactors
Theoretically, you could have a helium or carbon dioxide-cooled fast reactor. But these remain in the realm of paper reactors.
High Temperature Gas-Cooled Reactors
Helium is the main gas of interest for these reactors because it rarely absorbs neutrons and doesn't become radioactive. It can reach very high temperatures and obtain better heat engine efficiency because it is a gas with a low boiling point. It is also theoretically possible to run the helium through a turbine to produce electricity, eliminating the need for an additional fluid loop.
There was a 300 megawatt commercial helium-cooled reactor in Colorado, but it was shut down around the same time as Rancho Seco due to poor economics. The utility built a natural gas power plant to replace it. In practice, turbines with helium as the working fluid are challenging, and the plants use the helium to make steam. The main problem is that helium tends to leak out, and water tends to leak in, causing problems in the reactor loop.
Radiant Nuclear is the most interesting startup in this space. More on them below.
A Simpler Path
Are there designs that can offer simplicity, passive safety, and fewer/less tightly coupled systems? It turns out there are, and they are more than paper reactors.
KRUSTY is a 1-10 kilowatt reactor designed for space applications and deviates substantially from traditional designs.
The first difference is in heat transfer. It has no heat transfer fluid loops. Instead, heat pipes move heat from the reactor to the heat engine. Heat pipes have no moving parts and contain fluids like water, methanol, or sodium, depending on the temperature range. The electronics industry uses them to help cool devices. They can move a lot of heat because they utilize a fluid's latent heat. In KRUSTY's case, the reactor boils sodium which then condenses on the side touching the heat engine.[1] The liquid sodium flows back to the hot side through a wick. Heat pipes allow decoupling of the heat engine and reactor requirements.
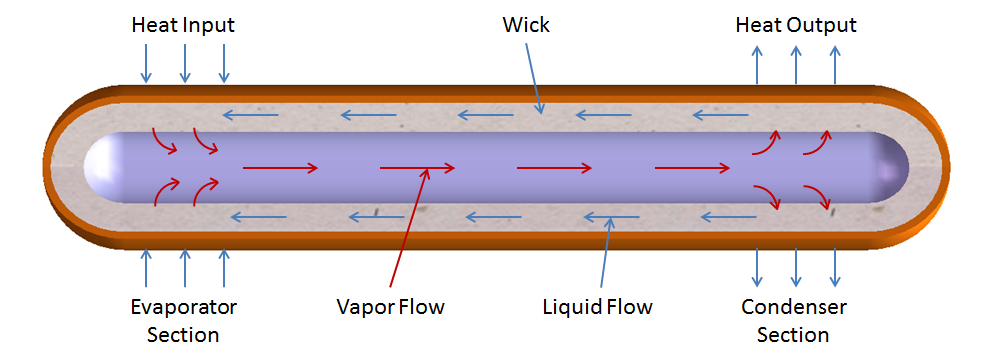
How a heat pipe works. Source: myheatsinks.com
KRUSTY uses a uranium metal-fueled fast reactor. Metals have excellent heat transfer that improves safety and increases heat flow to the heat pipes. The fuel has a strongly negative reactivity temperature coefficient. That means the chance that neutrons hit another fissile atom decreases as temperature increases because the metal expands. KRUSTY doesn't need any reactivity or fluid control systems as a result. Usually, reactors have to manage their reactivity with neutron poisons or control rods. Pressurized water reactors have incredibly complex systems to adjust the boron (a neutron poison) concentration in the reactor loop. It is an entire extra radioactive water storage and mixing complex. And all the previous reactor concepts we've seen have to regulate coolant flow. KRUSTY produces less power if the heat engine runs less because the fuel heats up and reactivity falls. The reactor is small enough to shed heat from nuclear decay to the surrounding air or radiate it into a vacuum.
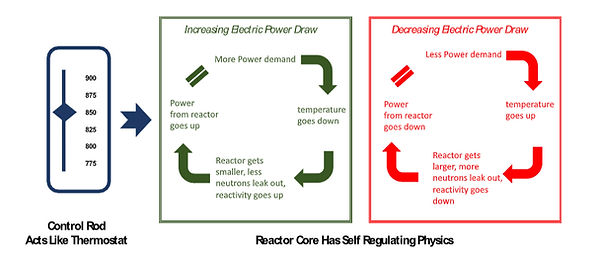
No controls required. Source: spacenukes.com
Another great advantage to a metal-fueled fast reactor is that modeling is easy. Moderators can add uncertainty and complexity to modeling risk. The simple design allows a small team to quickly model any scenarios regulators want to see or make adjustments on the fly.
The fuel can't start a chain reaction on its own. The design uses a beryllium neutron reflector to send neutrons back toward the fuel. That is an advantage for safe handling during manufacturing, testing, and assembly. Again, the simple nature of the fuel allows engineers to model this fact under many conditions with less work, giving confidence to regulators and others along the supply chain.
KRUSTY is too small-scale to be practical for most heat engines. The engineers selected a Stirling engine, which has few moving parts (a bonus for space applications) and is most competitive at smaller sizes. The combination of the fuel and heat pipes allows the hot side temperature of the heat engine to operate at 800C, which is higher than almost any other nuclear concept and improves efficiency.
Remarkably, it took 3.5 years to design, get approval, build, and test the reactor. The cost was under $20 million, while a previous space reactor concept cost $500 million in the 1980s dollars to create some stacks of paper. The focus on simplicity paid off.
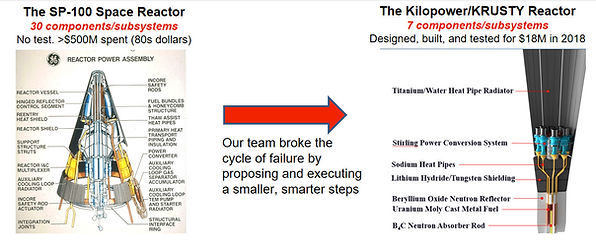
Costs increase exponentially with complexity Source: spacenukes.com
So what are the tradeoffs? The first is that fuel is expensive. Fast reactors need more to start, and fission products can lead to swelling. KRUSTY has WAY more fuel than it needs for a long-duration space mission to keep swelling to a minimum. In an interview, the lead engineers estimated it would probably run for hundreds of years at several kilowatts of power. The focus on KRUSTY was building an actual reactor, so the fuel choice had to be something already in production. The Y-12 defense complex at Oak Ridge National Lab cast KRUSTY's fuel at the premium price of $5 million. Y-12 makes highly-enriched uranium fuel for submarines and aircraft carriers. It is expensive. The other major limitation is this concept cannot scale over several megawatts because there is too much fuel and heat in a small area for the self-regulation to work.
Many space customers are happy to pay that price for KRUSTY's features. We wouldn't pay that on Earth. But, the design allows for evolution to more terrestrial-friendly options. A low-enriched uranium core that is too large for space applications could be cheaper. Or more traditional fuel pellets in tubes (called fuel pins) can be put into a stainless block monolith and still retain KRUSTY's self-regulation advantages. Fuel burnup can be much more aggressive since it is possible to refuel. Startups like Black Mesa Advanced Fusion are taking this approach, while the original KRUSTY engineers started Space Nukes.
Conventional wisdom is that nuclear plant size must be enormous to gain economies of scale. But heat pipes, neutron reflectors, fuel pins, and Stirling engines scale differently than turbines, compressors, heat exchangers, piping, and pumps. They could all see significant cost reductions through increasing manufacturing rates. It is compatible with other heat engines like thermoelectric generators. And small reactors can compete against diesel generators or retail electricity rates rather than the wholesale rates conventional nuclear power plants get paid. Nuclear's ace in the hole is energy density, and large power plants throw that away.
The most underrated aspect of KRUSTY and kilowatt scale reactors is their existence. Space probe engineers might like a higher-performance reactor, but those exist only on paper. Y-12 can crank out more fuel cores. Any terrestrial descendants will also benefit from existing.
Comparing Radiant and the Westinghouse eVinci
Radiant is building a 1.5 megawatt helium-cooled, graphite-moderated reactor with a separate supercritical CO2 power loop.
Westinghouse's 5-megawatt eVinci draws inspiration from KRUSTY and uses a more traditional fuel in a stainless steel monolith using heat pipes to power an open-loop Brayton cycle. Open-loop Brayton cycles compress air, heat it, and run it through a gas turbine. They are similar to simple-cycle gas turbine power plants or jet engines, so they are cheap and lightweight compared to most heat engine options. There are many changes to eVinci from KRUSTY, increasing risk. The fuel is completely different, moderated, and harder to model. The heat engine is conventional, but still requires testing.
The market for both is to replace diesel generators, and the power plants will be in shipping containers.
These designs use a fuel called TRISO, which is small uranium pellets coated in graphite and ceramics. Engineers designed it in the 1960s for gas-cooled reactors. TRISO has a low uranium density, which requires moderation in this context but is more challenging to melt than other fuel designs. eVinci uses a hydride moderator instead of the classic graphite. Let's look at how they will handle licensing.
Radiant
NRC's modernized processes are similar to how NASA certifies commercial providers for programs like Commercial Resupply, Commercial Crew, and NASA Launch Services missions. Probabilistic risk assessment is front and center, and a professional staff evaluates performance-based alternatives. SpaceX has an incredible ability to navigate these approvals with faster schedules and lower budgets than its competitors. How do they do it? SpaceX rapidly iterates, tests, and qualifies hardware as a supplement to its robust modeling capability. Their modeling and software tools allow iteration in the design space then rapid physical testing verifies and improves the models. While Boeing did not do even one full software integration test before its first (disastrous) commercial crew flight test, SpaceX ran at least one test on real hardware daily. The "hardware-in-the-loop" testing allows you "test like you fly," building confidence and generating an incredible amount of good data for the regulator as a side effect.
SpaceX veterans started Radiant. We know from a recent interview that they are already at it with rapid iteration and "hardware-in-the-loop" testing. They are currently focusing on the helium compressor and primary loop. It is a logical place to start, given the component's high risk and the ability to test immediately. They need tight data on their entire process because the helium loop is the primary way to remove heat from the reactor. Whether its runtime is 98% or 99% may not matter much for economics, but it plays a role in how much work backup systems have to do and the eventual risk score. They also have contracts to test their reactor components at Idaho National Lab. Radiant can ask for performance-based exceptions, and if NRC wants more data, then Radiant can bury them in truth from their existing tests.
In hindsight, the helium-cooled selection makes sense for Radiant because it is much easier to test and iterate than a lead or sodium design. Oklo is in a place where it needs to test, yet its design is challenging to piece apart. They have to build the full-size pool of sodium with all the requisite piping because there is no other way to see if the natural circulation works in all the edge cases. The easiest ways to add and remove heat from the system are steam and cooling water, but you'd have to take extra care to prevent sodium fires. Fluid freezing in pipes is a concern for prototypes. Lead isn't much better because of the poison risk. Iterations will be relatively slow.
Radiant's design has fewer passive safety features than most, relying on the fuel design and the small size to prevent overheating in an accident. That means their systems are less coupled and easier to test individually.
The control drums (similar to control rods) appear to be active control only. The reactor relies on the natural circulation of air to cool decay heat from the fuel, but it isn't clear whether the openings for air to enter are passively activated. The reactor should easily be able to meet risk standards even if they aren't passive. We know old-school LWRs with traditional fuel can exceed requirements. A small reactor with 1/1000 the fuel loading and intrinsically safer fuel should, too. And as you get smaller, you don't have enough nuclear material onboard to impact the surrounding population in an accident.
Westinghouse eVinci
eVinci's path to licensing also looks promising. In 2019 they engaged with the group (NRC, DOE, Southern Co.) working to modernize non-light water reactor regulations. The group went through the design to determine what initiating events the system would require for modeling. It is a beautiful thing to see statements like:
Because of the limited number of components in the
eVinci Micro-Reactor design that could be considered fire ignition sources, and the small size of
the plant, it is expected that a fire resulting from one of the few fire ignition sources in the plant
would have an impact very similar to the loss of the individual component.
And:
Because of the absence
of water-based systems in the design of the eVinci Micro-Reactor, it is expected that the flood
hazard is essentially eliminated by design.
And:
The simplicity of the eVinci Micro-Reactor design allows the four event trees that were initially
envisioned to address each of the IEs to be collapsed into one single event tree structure, with all
the system dependencies directly captured in the mitigation logic.
It seems as if most of eVinci's effort will hinge on better defining risk numbers for its unique components. It may still be painful for them if they don't have a robust testing campaign to tighten the inputs. KRUSTY went through an extensive testing process to meet the regulator's requirements on time.
The Final Tally
There are many great things about the eVinci concept. It should be easier to build and license, given its simplicity. Radiant has an enormous amount of components in comparison with its two fluid loops. But it is hard to bet against Radiant, given their testing mentality. You expect Westinghouse to somehow snatch defeat from the jaws of victory.
The main possible advantage of Radiant's reactor is that it is easier to scale into a large power plant. If this reactor is only Falcon 1, Falcon 9 and Falcon Heavy may come later.
Tackling The Future
Diving into the details reveals a lot of thorny issues. Plants often need experience to reach safety and capacity factor goals. Erasing all the rules and moving to 100% performance-based regulation won't magically fix the nuclear industry's economic woes. Nuclear engineering will stay difficult with many constraints. And we might need to help NRC hire better talent to reduce licensing costs as non-deterministic methods grow in importance. Work has gone into making existing plants viable but less into new reactors, especially non-light water reactors.
Complexity in design and operation exacerbates these issues. The less maintenance and labor your design needs and the more reliable it is, the easier ALARA is to meet. A simple plant is both easier to build and easier to license. A robust testing campaign improves design while also reducing regulatory risk. A simple reactor can have fewer possible adverse interactions, but decoupling components in the overall system matters for development speed.
Painfully simple designs like KRUSTY are what can work. How do we help make them cheaper and get a glorious nuclear future?
Fuel is the Elephant in the Room
Nuclear Fuel is Expensive
As we see with the tradeoffs between KRUSTY, eVinci, and traditional reactors, more expensive fuel can substitute for design complexity. If your power plant costs more money to build to take advantage of "cheap fuel," that fuel isn't cheap. You have to account for all costs. There is a continuum where heavy water reactors use the least refined fuel but have the most design complexity, and fast reactors like KRUSTY require higher quality fuel to lower complexity.
Fuel is more pricey than advertised for advanced reactors. They require more enrichment to meet design goals or need advanced fabrication like TRISO. Most designs envision long fuel cycles 5-10x longer than light water reactors to save labor and increase capacity factor. The cost is upfront and financed instead of ongoing, and financing for nuclear power plants isn't cheap.
The vast majority of fuel cost is in processing and manufacturing. Manufactured products costing thousands of dollars per kilogram often see significant price decreases as output grows. A rising demand/falling cost flywheel would make kilowatt scale reactors viable in many more applications. Enriching uranium is often energy-intensive, but electricity costs might fall significantly for designs that can utilize cheap power from sources like solar.
Not only is fuel expensive upfront, but handling spent fuel is a cost center. Calling it spent fuel is a misnomer because it is still usable! Many fissile elements can go into fast reactors or new fuel. There are also isotopes like Strontium-90 that could power nuclear batteries. Recycling fuel would leave little waste while enabling many new applications.
Lowering the cost of higher-quality fuel would be an accelerant for the entire industry.
Fuel Manufacturing and Technology Are Constrained
Many nuclear startups want to use fuel that isn't in mass production. There is a chicken and egg problem where no one is manufacturing it because no reactors are ready yet. The government is trying to make small amounts to allow testing by down blending old stocks. They are also trying to pay some companies to develop new production capacity. Fast growth may require vertical integration.
Some fast reactors can also "breed" new fuel. They can turn non-fissile U238 into fissile atoms by bombarding it with neutrons. There is the possibility of an entire ecosystem that uses one reactor's waste as the next reactor's fuel. We could be less than a decade away from solar PV being cheaper per megawatt-hour than the fuel cost for a light water reactor. Better use of uranium ore and fission products could be critical to nuclear's competitiveness.
The non-proliferation lobby opposes any attempts to recycle fuel or make enriched fuel cheaper. The concern comes from the dual-use nature of these technologies. Instead of performance-based targets, it is just "No." If there is no compromise, nuclear will likely remain a small part of our energy use.
If we extend probabilistic thinking to fuel supplies, paths open up. It isn't ideal that we have plutonium-containing fuel that will be radioactive for hundreds of thousands of years spread throughout the world. And it isn't great that our only commercial recycling technology is the PUREX process designed to make weapons material. There are alternatives like pyroprocessing that don't generate pure plutonium. Some studies suggest that pyroprocessing might already be cheaper than PUREX. It drinks electricity like water. Costs could fall further with less expensive electricity, closing the gap with mined uranium. Adopting processes like these could eliminate stored plutonium and reduce fast reactor fuel costs without being useful as a weapons technology.
New Reactors Need Testing Slots
You need testing locations if iterative testing is the easiest way to navigate performance-based regulations. Federal sites making it hard for startups and other non-traditional customers to get slots is nothing new. SpaceX had to develop its engine testing center in McGregor, TX (the site was home to a failed rocket startup) instead of getting access to existing test stands at Stennis Space Center. When no traditional launch site would give them space, SpaceX had to go to the Kwajalein Atoll in the Pacific Ocean to launch Falcon 1. Once SpaceX broke through, things finally loosened up. Half a dozen startups have leases for launch pads at various NASA and Air Force facilities, and startups like Relativity Space test engines at Stennis.
The US only has one facility for megawatt-scale testing, Idaho National Lab (INL). If INL abuses this monopoly out of laziness or status seeking to the extent that potential users refer to going there as the "INL Tax," it could bottleneck the entire nuclear ecosystem.
Part of KRUSTY's development speed advantage is that they had their choice of test sites. More facilities can accommodate kilowatt scale tests. The team used existing equipment at the Nevada National Security Site with only minor regulatory exceptions.
Making national labs more user-friendly has nothing to do with the usual nuclear regulation complaints, but it is critical for the industry's success. Pragmatic startups may need to start small enough that they can find their own Kwajalein Atoll.
The Evolutionary Paths We Want
We will likely get at least a few small modular light water reactors. And our existing fleet could run many decades longer where electricity market conditions justify their continued operation. Subsidies will keep those plants operating longer but also reduce pressure to continue the modernization of regulations.
Agile firms that can rapidly test and build their designs will play a role in the megawatt-scale remote power generation market and possibly graduate to larger plants where the economics work.
Those are all good things, but much of the future lies with KRUSTY-like kilowatt-scale systems. Nuclear has a power density problem that keeps it from powering our cars and planes. The shielding and heat engines are too heavy. The radiation and particles are harmful because they contain a lot of energy. The answer is to make solid-state technologies that convert heat and radiation into electricity. It is theoretically possible to turn gamma rays into electricity with something similar to a solar cell. Shielding gets lighter and generates electricity! It also brings new life to many isotopes that require too much shielding to be practical in radioisotope generators. In the meantime, kilowatt-scale systems can compete in smaller remote power applications and supplement solar microgrids. Further cost decreases could enable electricity customers to defect from the grid where solar is not feasible. Competing manufacturers promise a much more competitive industry than exists today, where incentives rarely encourage falling prices.
The endgame is a chunk of nuclear material that can regulate itself based on user demand, surrounded by energy-capturing devices that soak up every bit of emitted energy. Power density could exceed today's liquid fuels and batteries while having extreme energy density. We'd finally get our flying cars! Reactors that look like KRUSTY are on the path to that endgame.
- The heat pipe tubes are small and require very little sodium. The fire risk was labeled inconsequential in the regulatory analysis.
Can Nuclear Power Manage Another Comeback?
2022 September 7 Twitter Substack See all postsNuclear power survived a dark period in the 1980s by increasing output from existing power plants, can it build on that success to grow again? Thanks to Bill and Josh for answering an endless stream of questions. Any mistakes are my own.
Nuclear's Dark Period
Accidents and Poor Reliability Ding Nuclear
Safety concerns increased after events at Brown's Ferry (1975), Rancho Seco (1978), and Three Mile Island (1979). These events generated a long list of deterministic rules, most of which are still in the books. Construction times for already under construction plants increased. Three Mile Island usually takes the blame, but analysis shows only about 12% of retrofit costs were from changes specific to that incident. The combination of utilities spending more to improve reliability and changes from the other events in the late 1970s make up the balance.
Safety controls increased the difficulty of building new power plants and required upgrades at existing power plants. The average capacity factor was around 60% throughout the 1970s and 1980s. Nuclear power plants were more expensive while also being unreliable.
Competitors Get Unleashed
The government hamstrung nuclear's competitors in the 1960s and 1970s. Natural gas was heavily regulated, with new gas power plants de facto banned for some time. Coal is cheap at the mine but expensive to move, requiring barge or rail to keep prices reasonable. Regulated railroads were pricey.
The early 1980s saw the deregulation of both natural gas and railroads. Natural gas replaced underperforming power plants like Rancho Seco. Cheaper rail costs made existing coal plants cheaper to run and mitigated the pain of new laws to reduce sulfur dioxide emissions. Many utilities found they could ditch local, high-sulfur coal and buy low-sulfur coal from the Powder River Basin in Wyoming. Prices in a sulfur dioxide cap and trade scheme ended up being a fraction of the expected cost.
Source: sbecouncil.org
Source: EIA
Nuclear power's competitors rapidly improved their position in the market.
Demand Slows
Electricity growth was in the high single digits going into the 1970s, forcing utilities to build power plants like crazy. Demand growth slowed for reasons like efficiency boosting laws.
Source: EIA
The need for new power plants declined.
Increasing Output Delayed Need for New Power Plants
From the 1980s to today, the capacity factor of US nuclear power plants increased from <60% to >90%. The improved capacity factor meant that utilities got one free power plant for every two existing ones. Many of the expansion plans called for new reactors at existing facilities. The increased output removed the need for new reactors.
Source: Whatisnuclear.com
The story of how the industry did this involves better-managed utilities, a strong effort from the industry group (INPO), and regulation changes.
The Nuclear Industry's Turnaround
Institute of Nuclear Power Operations
The nuclear industry funds the Institute of Nuclear Power Operations (INPO) to promote safety and reliability. INPO started in 1979 following the Three Mile Island accident. It conducts regular inspections at all nuclear power plants, and many INPO employees are "on loan" from the utilities. It rates plant performance based on inspections and shares findings and best practices with all members, but not the public. INPO holds its members to a standard of excellence, going much further than the NRC, which only manages safety standards.
It may seem strange to have an organization like this, especially in the United States. But the nuclear industry was 100% regulated utilities with territorial monopolies in 1979. There are only a few designs, so sharing information has great benefits with no competition downsides. Utilities take INPO very seriously and often loan their best employees for tours of duty there.
INPO recognized right away that well-run plants are both safe and reliable. Human factors and organizational culture are points of intense focus. Accidents or poor economics could end the industry. Accidents are a more immediate threat because regulated monopolies own most nuclear power plants, and politicians are willing to dole out subsidies. Preventing accidents requires constant vigilance; one laggard could ruin the entire industry. There is a symbolic carving of "Excellence" in front of INPO's headquarters, with the "E" unfinished.
Another benefit of INPO is to create a powerful interest group to counter anti-nuclear groups like the "Union of Concerned Scientists" lobbying the NRC. In some cases, like worker training standards, NRC declined to create rules as long as utilities followed INPO's recommendations. INPO also sends its inspection data to the NRC.
In a 1985 update, we see that the industry was already achieving cultural and operational improvements in many areas:
Plant capacity factors are a lagging indicator and would begin a long climb in the late 1980s. One paradigm exemplifies the changes in the nuclear industry brought by utilities and INPO: Probabilistic Risk Assessments.
How Probabilistic Risk Assessments Change the Game
Probabilistic risk assessments (PRAs) emerged in 1975 and increased in prominence until full adoption in 1995. These assessments utilize a fault tree approach. They model a triggering event and calculate the probability that each safety feature will succeed in preventing core damage, a release to the environment, and an impact on the public. The standard for preventing core damage is one event in 10,000 reactor years and one in 100,000 reactor years for a release. The US currently has 93 reactors running, so we expect a core damage event every 107 years and a release every 1070 years. In practice, most plants exceed this margin by a factor of two.
How PRAs work. Source: NRC
The nuclear industry's adoption of PRAs changed the mindset of how to operate the plants. There was a rigid hierarchy of "safety equipment" and "non-safety equipment." The mentality inevitably led to a focus on safety equipment at the expense of plant reliability. Once operators started using PRAs, they discovered that many "non-safety" pieces of equipment were safety barriers and that the safest way to run a plant is at design conditions. Startups and shutdowns are often the highest risk periods for any industrial facility, nuclear power plants included.
PRAs better aligned operating costs and safety for the industry. Better reliability lowers costs for mostly fixed-cost nuclear power plants.
A pathway for increasing plant reliability was doing much more maintenance while the plant was online. The PRAs give utilities a guide on what equipment can be taken offline for repair or preventive maintenance on any day without increasing risk above the threshold. It avoids scenarios where you might accidentally take several barriers offline at once.
Time offline for fueling and repairs also decreased dramatically. There was less maintenance during planned outages, and the industry improved outage planning to complete tasks faster.
Source
One story shows the complexity of nuclear engineering and the change the PRA mindset brought. Stellite is a metal alloy that is great for making parts of valves like seats. But Stellite contains cobalt which can form Cobalt-60 when hit with neutrons. Cobalt-60 releases very high-energy gamma rays that can harm workers. Fluid can erode parts of the valve while flowing past. Those particles go through the reactor, get hit with neutrons, then settle down into parts of the systems like traps. When workers clean these areas, they can get exposed to high-energy radiation. The original directive from regulators was to ban using Stellite in equipment with possible exposure to neutrons. Plants had to use valves that required more maintenance and were more likely to leak. Risk calculations uncovered that worker exposure would be lower while using Stellite under some scenarios because of reduced maintenance and testing. The cost goes down while safety and reliability increase.
Interaction with Traditional Rules and PRAs
Many of the deterministic rules still exist. Everyone has to follow the rules, but PRAs are like a relief valve. For instance, there is a rule that safety-related equipment cannot be out of service for over 72 hours, or the plant must shut down. But there is often equipment that is hard to access and service. Repair in under 72 hours isn't physically possible. The utility can ask for an exception from the NRC. Keeping the plant online is likely safer if the utility can fix it in a reasonable amount of time. The PRA process provides evidence that allows the exception.
Following the full adoption of PRAs in 1995, NRC now provides performance-based alternatives for any new rule and often adds them to old regulations if desired by utilities. The switch to performance from deterministic rules isn't always easy or a low-cost option. NFPA 805 is an effort that started in the mid-2000s to move fire protection from deterministic to risk-informed, performance-based regulation. It is to be followed by similar conversions to seismic and flooding risks. A conference between the utilities and NRC about early implementation is illuminating. The early plants to pilot the process, like Oconee and Harris, saw costs much higher than meeting deterministic rules. Since fires can start in many places, the PRAs had thousands of initiating events to analyze. Completing the work took ~50,000 hours per plant. Part of the cost problem was that some initial variables for calculating risk were too conservative by a factor of 10. The utilities responded by requesting many exceptions and providing alternatives that led to lots of back and forth between the utilities and NRC, using many engineering hours. Both sides agreed to changes to try to make it easier for the rest of the nuclear fleet to switch.
Light Water Reactors are Labor Intensive
Light water reactors have hundreds of engineering subsystems. One way to think about their design is that they use simple parts but have a complex overall architecture. A multi-billion dollar chemical complex might have less than ten non-management engineers. A light water nuclear power plant needs hundreds. Even without regulation, the power plants still require many of these engineers. An engineer at a refinery doesn't have to worry about his isotopes changing! That simplifies a lot of work. A carbon steel pipe with oil in it might last hundreds of years. Piping and equipment exposed to neutrons, radiation, or hydrogen and oxygen from electrolysis in the reactor need more maintenance and care. It takes a lot of workers to complete the required maintenance safely.
The regulation does add work. It takes a lot of engineering resources to complete PRAs. And having PRAs requires competent engineers and scientists to work for the NRC.
Less regulation and better regulation would certainly reduce costs, but the impact on operating costs for existing plants is less than we'd hope. Many plants in deregulated markets will still struggle when electricity prices are low from cheap gas or renewables, especially when they face repair bills like replacing steam generators.
Is ALARA Making Nuclear Power More Expensive?
The nuclear industry aims to keep radiation exposure As Low As is Reasonably Achievable (ALARA). ALARA is an example among critics of how the government won't ever let nuclear be cheap. But would things change if ALARA went away?
First, anyone that has worked in a nuclear power plant or a large chemical processing facility knows how specialized these workers are. At the chemical plant where I worked, the average employee tenure was around 18 years. The norm is to work your entire life at one facility. There are few others like it, and the pay is higher due to the quality of employees required and the skills and experience you develop. The workforce is unionized, or owners fear unionization.
Another thing that becomes apparent is that these facilities' complexity and maintenance requirements require an extremely high-performance culture. The expectation is that the plant always runs and only bad things can happen. For owners, many deviations have extreme tail risks where workers die; or the population outside the plant gates sees impacts.
You can't expect employees to participate in this culture if you don't value their health and lives. Just like the business expectation is that there will be continuous improvement in plant operations (nothing is ever good enough), the only acceptable long-term goal for safety and health is zero impact.
Furthermore, accidents are non-linear. People can die falling from twelve inches. If you want zero workplace deaths, you have to eliminate all falls. Radiation exposure also has non-linearities. A safe exposure outside your body might not be safe if you accidentally stick your pen in your mouth while filling out paperwork. Other factors can compound so that an employee that makes a mistake and exposes themselves to radiation with a large effective dose. Like with falls, the best way to prevent the risk of harm is to push exposure risk as low as possible. It is unreasonable to compare the risk to a job like a flight attendant because their radiation exposure does not have the same non-linearity.
The reality on the ground is that nuclear organizations are committed to ALARA from top to bottom, and they would be regardless of regulation. As an antidote, you can read the famous business case study of how Alcoa turned its business around by focusing on safety.
Summarizing Nuclear's Progress
The industry took unreliable plants with unacceptable safety and turned them into the safe, reliable plants we know today. Collaboration between utilities, INPO, and NRC to create performance-based alternatives was important. But these changes aren't a silver bullet.
What does this experience tell us about building new reactors?
Lessons For Future Reactors
Many people are upset that we have built more paper reactors than real ones in recent decades. They blame the NRC licensing process and ALARA while assuming that the economics would work themselves out without regulation. There is no avoiding the details of nuclear engineering to find something closer to the truth. I'll walk you through the tradeoffs nuclear engineers face and the resulting design choices.
I'm going to accept that future reactors will go through probabilistic risk analysis. So complicated designs will be harder to build, more expensive to maintain, and more challenging to license. A safe, complex design is just as costly to license as an unsafe, complex design. And an extremely safe and simple design might be cheap to license in comparison. PRA cost and effort are related to complexity, not safety.
It's All About the Neutrons
Fission is when an atom splits into two smaller atoms, often releasing neutrons and other radiation. Only certain isotopes are fissile. They naturally undergo fission slowly but seldom have fission chain reactions like atom bombs or nuclear power plants. Uranium-235 (U235) is the most common fuel because we can mine it easily.
To create a chain reaction, the neutrons from a splitting atom must hit other atoms causing them to split and release more neutrons. Engineers consider how likely a neutron collision with another fissile atom is when designing nuclear fuel. There need to be enough atoms in a small space. Each fissile element has a minimum mass required to sustain a chain reaction (depending on conditions). The speed of neutrons is a chief consideration. Atoms have different "cross-sections," where they are more likely to collide with neutrons at certain speeds than others. Non-fissile atoms turn into a different isotope when they capture a neutron instead of splitting.
U235 is much more likely to capture slow neutrons but produces fast neutrons when it splits. Most existing nuclear reactors use a moderator to slow neutrons down, reducing the amount of uranium needed to start a reaction by increasing the chance of collisions. Hydrogen is the best moderator because it has the same mass as neutrons and absorbs more kinetic energy than larger atoms. Conveniently, there are a lot of hydrogen atoms in water molecules, and most reactors use water as a moderator. Graphite is the next most popular choice.
Good moderators also need to avoid capturing neutrons. Captured neutrons can't participate in a chain reaction and usually make whatever is capturing them radioactive. "Light" water is a mediocre moderator because its hydrogen atoms can capture neutrons and become deuterium. Heavy water reactors use only deuterated water to improve performance by reducing moderator capture of neutrons.
Some reactor designs have no moderator and are known as fast reactors. They can use fuel more efficiently because some fissile isotopes created by neutron bombardment only capture fast neutrons. Moderated reactors leave these isotopes in their spent fuel, and the isotopes can stay radioactive for hundreds of thousands of years. Fast reactor waste is often safe after a few hundred years. Because the main fissile isotope (U235) is less likely to capture fast neutrons, fast reactors need more starting fuel, among other complications.
A central tension in nuclear engineering is that the fluid heated near the reactor has very different requirements than the fluid that powers the heat engine. Most designs have a reactor loop and a power generation loop, while other thermal power plants only have a power generation loop. The neutrons are why many concepts have helium, sodium, molten salt, or lead in the reactor loop.
Control rods contain materials that capture neutrons easily, like boron. Removing the rod increases neutrons available to sustain chain reactions.
The Logic of Water Moderated Reactors
Using water as a moderator has many advantages. It has a low freezing point, is well understood, pumps readily, and is an excellent heat transfer fluid.
The limitations are that it has a low boiling point and becomes radioactive in a reactor. The low boiling point requires pressurized water reactors (PWRs) and boiling water reactors (BWRs) to use high pressure to reach a reasonable temperature and heat engine efficiency. Light water reactors must also use enriched fuel to overcome water's neutron absorption that stymies chain reactions. Their fuel is typically 3%-5% U235 vs. 0.7% for natural uranium.
Heavy water-moderated reactors (HWRs) like Canada's CANDU are strange beasts. They can use natural uranium since heavy water is an excellent moderator. They also don't require a reactor pressure vessel. The fuel and coolant are in pipes submerged in heavy water. Theoretically, you could use a gas or organic coolant, but CANDU doesn't. It runs like a pressurized water reactor with water coolant and a steam generator where the coolant heats a clean water loop. HWRs require a much larger reactor, and heavy water is expensive. Canada has lots of uranium, no nuclear weapons program to share enrichment facilities/expertise, and struggled to build large pressure vessels during reactor development. CANDU fits within those requirements.
Again, water-moderated reactors have many parts and a deceiving amount of complexity. But the components are pumps, valves, machined parts, water-water heat exchangers, and turbines that are relatively straightforward compared to non-water coolant designs.
The Rise of Passive Safety in Gen III and Gen IV Reactors
Reactor safety took center stage after accidents like Three Mile Island and Chernobyl. The most popular concept is to use passive safety systems instead of active ones. Passive safety means making changes like using the natural circulation of coolant to cool the reactor instead of pumps. These changes can make the reactors a few orders of magnitude safer while decreasing part count.
The negative is that the plants require more upfront engineering and much tighter construction tolerances than Gen I and II designs. Disaster can strike when attempting to build such facilities with regular construction practices like incomplete detailed drawings at the start of construction (cough, VC Summer, cough). Passive safety reactors don't necessarily have fewer initiating events in PRAs, and models need more precision to complete the trees adequately. Complexities around radioactive fluid, heat from radioactive decay of fuel, and damage from external events still need modeling.
It may seem counterintuitive that these plants are harder to build with fewer parts, but passive systems are more sensitive to changes than active systems. Small changes in piping can change the natural circulation rate. An engineer can complete the basic design for an active cooling loop on a few sheets of paper. Moving piping during construction is no big deal because the engineer undoubtedly oversized the pumps to handle small increases in pressure drop. That probably happened in the field, on the fly, for early reactors. Modeling natural circulation in complex piping requires a computer simulation, and you'd have to rerun the entire model to check if the circulation rate remains acceptable after any change. Passive safety systems can tightly couple subsystem design.
A large Gen-III facility requires unprecedented detail for one of the most complex construction projects humans have ever undertaken. The decision to use some modular components for the AP1000 only exacerbated the challenge. It is funny that Westinghouse and CBI needed more detailed engineering to succeed than NRC required for licensing.
Once we consider the complexity paired with the loose coupling of older designs, it starts to make sense how some plants in the 1960s looked so inexpensive to build. They had lower-paid workers building labor-intensive designs that were tolerant of construction errors, while lacking many safety and reliability features that facility owners retrofitted later. And construction companies built the lowest-price plants on fixed-price contracts where they took a bath due to cost overruns. You couldn't repeat that today due to labor costs alone. And as a sanity check, we see that today's vastly simpler gas power plants cost more than some of the claimed 1960s prices you see in papers like Lovering et al.
Light Water Small Modular Reactors
These issues led to the desire for smaller reactors built in factories, known as Small Modular Reactors (SMRs). SMRs typically range from ~50 megawatt to ~300 megawatt. The idea is that the extra engineering will be spread over many identical units while factory construction can better accommodate tighter tolerances.
They lose scale in items like vessels, pumps, turbines, and heat exchangers but gain factory efficiency. No one expects these designs to set records for low-price electricity, but they do have orders in places where electricity is expensive.
The NRC recently (2022) approved the first light water SMR design from the startup NuScale.
Advanced Non-Light Water Reactors
It wasn't clear which designs would be the best early in the nuclear era. There was lots of experimentation, and we built gas-cooled reactors, metal-cooled fast reactors, etc. All of the light water reactor alternatives proved to be uneconomic. When the industry started modernizing regulations, every commercial reactor operating was a light water reactor. And those are the only regulatory codes that were updated. Once SMRs appeared on the horizon, the NRC focused on modernizing regulations for light water small modular reactors, like NuScale.
Then startups came out of the woodwork wanting to build non-light water reactors. So the slow machinery of bureaucracy has started on programs to modernize codes for these reactors. The most logical reasons for the re-emergence of these designs have been falling wholesale electricity prices or a desire to utilize fast reactor fuel cycle advantages. Some non-light water reactors can have a fraction of the subsystems as a light water reactor and better efficiency but are more technologically challenging and expensive to maintain. The startups hope they can overcome the technical and economic challenges to better compete in competitive electricity markets.
Sodium-Cooled Fast Reactors
Fast reactors using a liquid coolant have two popular options, one being sodium. Like moderated reactors, the coolant shouldn't capture neutrons. But the atom also needs to be relatively big, so neutrons bounce right off and maintain speed. Compact fast reactor cores need fluids with exceptional heat transfer. Sodium fits the bill and has a high boiling point, allowing the reactor to reach higher temperatures at atmospheric pressure.
The downsides are rough. Sodium catches on fire when exposed to air and violently explodes in contact with water. The freezing point is high, so care has to be taken to keep it from freezing in pipes, pumps, and valves. Natural circulation of the coolant in pools is a feature of almost all designs to improve safety and reduce the risk of freezing in equipment.
One of the first US nuclear submarines tested a sodium-cooled reactor. Admiral Rickover had this to say:
The admiral had it ripped out and replaced with a light water reactor.
The BN-600 is a long-running, commercial sodium-cooled reactor in Russia. It suffered a few dozen fires early in its life but hasn't had one in decades. The plant's lifetime capacity factor is ~75%, but its recent performance is in the high 80s. Lengthy fueling outages prevent capacity factor from increasing much more. Russia recently completed the BN-800. The motivation is to use a "closed-fuel cycle" (mixed uranium and plutonium) and burn weapons-grade plutonium.
Success is possible, especially with pool-style designs, but complexity and cost are still high. The power plants took over a decade to build and have three fluid loops, a sodium pool around the reactor and a second sodium loop that transfers heat from the reactor pool to a steam generator.
GE is designing a conventional sodium-cooled fast reactor similar to the BN-600 and the Experimental Breeder Reactor II.
TerraPower is a US startup working on a 345 megawatt sodium-cooled fast reactor. They also want to attach molten salt storage to the facility to allow the plant to deliver more power at peak times. Combining two challenging technologies like that is pretty absurd. But they recently raised another $750 million, so some disagree with my assertion.
Oklo is designing a 1.5 megawatt sodium-cooled fast reactor with a supercritical CO2 power cycle. Using CO2 working fluid in a closed Brayton cycle can improve efficiency and cost over steam turbines. It also eliminates the potential for water contact. Oklo could build larger power plants based on the design if successful.
The NRC canceled Oklo's application after the NRC was unhappy with their progress (while still allowing them to reapply later). It's clear that Oklo didn't provide the detailed engineering NRC requires in its licensing activities. Oklo also chose a strange licensing route. They avoided the process that NRC is working on to modernize licensing for non-LWRs and submitted alternative risk calculation methods. The NRC asked them to show their work, and Oklo did not provide the details to the NRC's satisfaction about topics like "maximum credible accident size." As we've seen before, performance-based is an option. But it can be engineering intensive when dealing with complex reactor configurations like sodium-cooled fast reactors and mostly unproven power cycles like a CO2 Brayton cycle.
The appeal of sodium-cooled fast reactors is they are the only fast reactors with a long operating history. That makes them a natural choice for deploying fast reactors that can utilize waste from light water reactors. But they are still challenging to build and prototype. And they aren't likely to set cost records.
Lead-Cooled Fast Reactors
Lead is the other main option for fast reactors using liquid coolant. It is poisonous, but at least it doesn't catch on fire! Reduction of fire risk could allow the power loop heat exchanger to be in the lead pool, eliminating an extra fluid loop that traditional sodium-cooled reactors require to keep water away from the reactor. It has similar drawbacks with a high freezing point, and its heat transfer properties aren't as good as sodium. Corrosion is a concern, as well. Like sodium, pool-style designs are popular.
The Soviet Alpha-Class submarines used lead-cooled fast reactors. Russia has plans to build several commercial plants using the technology. Westinghouse has a lead-cooled concept, but interest seems to be more lukewarm in the West.
Gas-Cooled Fast Reactors
Theoretically, you could have a helium or carbon dioxide-cooled fast reactor. But these remain in the realm of paper reactors.
High Temperature Gas-Cooled Reactors
Helium is the main gas of interest for these reactors because it rarely absorbs neutrons and doesn't become radioactive. It can reach very high temperatures and obtain better heat engine efficiency because it is a gas with a low boiling point. It is also theoretically possible to run the helium through a turbine to produce electricity, eliminating the need for an additional fluid loop.
There was a 300 megawatt commercial helium-cooled reactor in Colorado, but it was shut down around the same time as Rancho Seco due to poor economics. The utility built a natural gas power plant to replace it. In practice, turbines with helium as the working fluid are challenging, and the plants use the helium to make steam. The main problem is that helium tends to leak out, and water tends to leak in, causing problems in the reactor loop.
Radiant Nuclear is the most interesting startup in this space. More on them below.
A Simpler Path
Are there designs that can offer simplicity, passive safety, and fewer/less tightly coupled systems? It turns out there are, and they are more than paper reactors.
KRUSTY is a 1-10 kilowatt reactor designed for space applications and deviates substantially from traditional designs.
The first difference is in heat transfer. It has no heat transfer fluid loops. Instead, heat pipes move heat from the reactor to the heat engine. Heat pipes have no moving parts and contain fluids like water, methanol, or sodium, depending on the temperature range. The electronics industry uses them to help cool devices. They can move a lot of heat because they utilize a fluid's latent heat. In KRUSTY's case, the reactor boils sodium which then condenses on the side touching the heat engine.[1] The liquid sodium flows back to the hot side through a wick. Heat pipes allow decoupling of the heat engine and reactor requirements.
How a heat pipe works. Source: myheatsinks.com
KRUSTY uses a uranium metal-fueled fast reactor. Metals have excellent heat transfer that improves safety and increases heat flow to the heat pipes. The fuel has a strongly negative reactivity temperature coefficient. That means the chance that neutrons hit another fissile atom decreases as temperature increases because the metal expands. KRUSTY doesn't need any reactivity or fluid control systems as a result. Usually, reactors have to manage their reactivity with neutron poisons or control rods. Pressurized water reactors have incredibly complex systems to adjust the boron (a neutron poison) concentration in the reactor loop. It is an entire extra radioactive water storage and mixing complex. And all the previous reactor concepts we've seen have to regulate coolant flow. KRUSTY produces less power if the heat engine runs less because the fuel heats up and reactivity falls. The reactor is small enough to shed heat from nuclear decay to the surrounding air or radiate it into a vacuum.
No controls required. Source: spacenukes.com
Another great advantage to a metal-fueled fast reactor is that modeling is easy. Moderators can add uncertainty and complexity to modeling risk. The simple design allows a small team to quickly model any scenarios regulators want to see or make adjustments on the fly.
The fuel can't start a chain reaction on its own. The design uses a beryllium neutron reflector to send neutrons back toward the fuel. That is an advantage for safe handling during manufacturing, testing, and assembly. Again, the simple nature of the fuel allows engineers to model this fact under many conditions with less work, giving confidence to regulators and others along the supply chain.
KRUSTY is too small-scale to be practical for most heat engines. The engineers selected a Stirling engine, which has few moving parts (a bonus for space applications) and is most competitive at smaller sizes. The combination of the fuel and heat pipes allows the hot side temperature of the heat engine to operate at 800C, which is higher than almost any other nuclear concept and improves efficiency.
Remarkably, it took 3.5 years to design, get approval, build, and test the reactor. The cost was under $20 million, while a previous space reactor concept cost $500 million in the 1980s dollars to create some stacks of paper. The focus on simplicity paid off.
Costs increase exponentially with complexity Source: spacenukes.com
So what are the tradeoffs? The first is that fuel is expensive. Fast reactors need more to start, and fission products can lead to swelling. KRUSTY has WAY more fuel than it needs for a long-duration space mission to keep swelling to a minimum. In an interview, the lead engineers estimated it would probably run for hundreds of years at several kilowatts of power. The focus on KRUSTY was building an actual reactor, so the fuel choice had to be something already in production. The Y-12 defense complex at Oak Ridge National Lab cast KRUSTY's fuel at the premium price of $5 million. Y-12 makes highly-enriched uranium fuel for submarines and aircraft carriers. It is expensive. The other major limitation is this concept cannot scale over several megawatts because there is too much fuel and heat in a small area for the self-regulation to work.
Many space customers are happy to pay that price for KRUSTY's features. We wouldn't pay that on Earth. But, the design allows for evolution to more terrestrial-friendly options. A low-enriched uranium core that is too large for space applications could be cheaper. Or more traditional fuel pellets in tubes (called fuel pins) can be put into a stainless block monolith and still retain KRUSTY's self-regulation advantages. Fuel burnup can be much more aggressive since it is possible to refuel. Startups like Black Mesa Advanced Fusion are taking this approach, while the original KRUSTY engineers started Space Nukes.
Conventional wisdom is that nuclear plant size must be enormous to gain economies of scale. But heat pipes, neutron reflectors, fuel pins, and Stirling engines scale differently than turbines, compressors, heat exchangers, piping, and pumps. They could all see significant cost reductions through increasing manufacturing rates. It is compatible with other heat engines like thermoelectric generators. And small reactors can compete against diesel generators or retail electricity rates rather than the wholesale rates conventional nuclear power plants get paid. Nuclear's ace in the hole is energy density, and large power plants throw that away.
The most underrated aspect of KRUSTY and kilowatt scale reactors is their existence. Space probe engineers might like a higher-performance reactor, but those exist only on paper. Y-12 can crank out more fuel cores. Any terrestrial descendants will also benefit from existing.
Comparing Radiant and the Westinghouse eVinci
Radiant is building a 1.5 megawatt helium-cooled, graphite-moderated reactor with a separate supercritical CO2 power loop.
Westinghouse's 5-megawatt eVinci draws inspiration from KRUSTY and uses a more traditional fuel in a stainless steel monolith using heat pipes to power an open-loop Brayton cycle. Open-loop Brayton cycles compress air, heat it, and run it through a gas turbine. They are similar to simple-cycle gas turbine power plants or jet engines, so they are cheap and lightweight compared to most heat engine options. There are many changes to eVinci from KRUSTY, increasing risk. The fuel is completely different, moderated, and harder to model. The heat engine is conventional, but still requires testing.
The market for both is to replace diesel generators, and the power plants will be in shipping containers.
These designs use a fuel called TRISO, which is small uranium pellets coated in graphite and ceramics. Engineers designed it in the 1960s for gas-cooled reactors. TRISO has a low uranium density, which requires moderation in this context but is more challenging to melt than other fuel designs. eVinci uses a hydride moderator instead of the classic graphite. Let's look at how they will handle licensing.
Radiant
NRC's modernized processes are similar to how NASA certifies commercial providers for programs like Commercial Resupply, Commercial Crew, and NASA Launch Services missions. Probabilistic risk assessment is front and center, and a professional staff evaluates performance-based alternatives. SpaceX has an incredible ability to navigate these approvals with faster schedules and lower budgets than its competitors. How do they do it? SpaceX rapidly iterates, tests, and qualifies hardware as a supplement to its robust modeling capability. Their modeling and software tools allow iteration in the design space then rapid physical testing verifies and improves the models. While Boeing did not do even one full software integration test before its first (disastrous) commercial crew flight test, SpaceX ran at least one test on real hardware daily. The "hardware-in-the-loop" testing allows you "test like you fly," building confidence and generating an incredible amount of good data for the regulator as a side effect.
SpaceX veterans started Radiant. We know from a recent interview that they are already at it with rapid iteration and "hardware-in-the-loop" testing. They are currently focusing on the helium compressor and primary loop. It is a logical place to start, given the component's high risk and the ability to test immediately. They need tight data on their entire process because the helium loop is the primary way to remove heat from the reactor. Whether its runtime is 98% or 99% may not matter much for economics, but it plays a role in how much work backup systems have to do and the eventual risk score. They also have contracts to test their reactor components at Idaho National Lab. Radiant can ask for performance-based exceptions, and if NRC wants more data, then Radiant can bury them in truth from their existing tests.
In hindsight, the helium-cooled selection makes sense for Radiant because it is much easier to test and iterate than a lead or sodium design. Oklo is in a place where it needs to test, yet its design is challenging to piece apart. They have to build the full-size pool of sodium with all the requisite piping because there is no other way to see if the natural circulation works in all the edge cases. The easiest ways to add and remove heat from the system are steam and cooling water, but you'd have to take extra care to prevent sodium fires. Fluid freezing in pipes is a concern for prototypes. Lead isn't much better because of the poison risk. Iterations will be relatively slow.
Radiant's design has fewer passive safety features than most, relying on the fuel design and the small size to prevent overheating in an accident. That means their systems are less coupled and easier to test individually.
The control drums (similar to control rods) appear to be active control only. The reactor relies on the natural circulation of air to cool decay heat from the fuel, but it isn't clear whether the openings for air to enter are passively activated. The reactor should easily be able to meet risk standards even if they aren't passive. We know old-school LWRs with traditional fuel can exceed requirements. A small reactor with 1/1000 the fuel loading and intrinsically safer fuel should, too. And as you get smaller, you don't have enough nuclear material onboard to impact the surrounding population in an accident.
Westinghouse eVinci
eVinci's path to licensing also looks promising. In 2019 they engaged with the group (NRC, DOE, Southern Co.) working to modernize non-light water reactor regulations. The group went through the design to determine what initiating events the system would require for modeling. It is a beautiful thing to see statements like:
And:
And:
It seems as if most of eVinci's effort will hinge on better defining risk numbers for its unique components. It may still be painful for them if they don't have a robust testing campaign to tighten the inputs. KRUSTY went through an extensive testing process to meet the regulator's requirements on time.
The Final Tally
There are many great things about the eVinci concept. It should be easier to build and license, given its simplicity. Radiant has an enormous amount of components in comparison with its two fluid loops. But it is hard to bet against Radiant, given their testing mentality. You expect Westinghouse to somehow snatch defeat from the jaws of victory.
The main possible advantage of Radiant's reactor is that it is easier to scale into a large power plant. If this reactor is only Falcon 1, Falcon 9 and Falcon Heavy may come later.
Tackling The Future
Diving into the details reveals a lot of thorny issues. Plants often need experience to reach safety and capacity factor goals. Erasing all the rules and moving to 100% performance-based regulation won't magically fix the nuclear industry's economic woes. Nuclear engineering will stay difficult with many constraints. And we might need to help NRC hire better talent to reduce licensing costs as non-deterministic methods grow in importance. Work has gone into making existing plants viable but less into new reactors, especially non-light water reactors.
Complexity in design and operation exacerbates these issues. The less maintenance and labor your design needs and the more reliable it is, the easier ALARA is to meet. A simple plant is both easier to build and easier to license. A robust testing campaign improves design while also reducing regulatory risk. A simple reactor can have fewer possible adverse interactions, but decoupling components in the overall system matters for development speed.
Painfully simple designs like KRUSTY are what can work. How do we help make them cheaper and get a glorious nuclear future?
Fuel is the Elephant in the Room
Nuclear Fuel is Expensive
As we see with the tradeoffs between KRUSTY, eVinci, and traditional reactors, more expensive fuel can substitute for design complexity. If your power plant costs more money to build to take advantage of "cheap fuel," that fuel isn't cheap. You have to account for all costs. There is a continuum where heavy water reactors use the least refined fuel but have the most design complexity, and fast reactors like KRUSTY require higher quality fuel to lower complexity.
Fuel is more pricey than advertised for advanced reactors. They require more enrichment to meet design goals or need advanced fabrication like TRISO. Most designs envision long fuel cycles 5-10x longer than light water reactors to save labor and increase capacity factor. The cost is upfront and financed instead of ongoing, and financing for nuclear power plants isn't cheap.
The vast majority of fuel cost is in processing and manufacturing. Manufactured products costing thousands of dollars per kilogram often see significant price decreases as output grows. A rising demand/falling cost flywheel would make kilowatt scale reactors viable in many more applications. Enriching uranium is often energy-intensive, but electricity costs might fall significantly for designs that can utilize cheap power from sources like solar.
Not only is fuel expensive upfront, but handling spent fuel is a cost center. Calling it spent fuel is a misnomer because it is still usable! Many fissile elements can go into fast reactors or new fuel. There are also isotopes like Strontium-90 that could power nuclear batteries. Recycling fuel would leave little waste while enabling many new applications.
Lowering the cost of higher-quality fuel would be an accelerant for the entire industry.
Fuel Manufacturing and Technology Are Constrained
Many nuclear startups want to use fuel that isn't in mass production. There is a chicken and egg problem where no one is manufacturing it because no reactors are ready yet. The government is trying to make small amounts to allow testing by down blending old stocks. They are also trying to pay some companies to develop new production capacity. Fast growth may require vertical integration.
Some fast reactors can also "breed" new fuel. They can turn non-fissile U238 into fissile atoms by bombarding it with neutrons. There is the possibility of an entire ecosystem that uses one reactor's waste as the next reactor's fuel. We could be less than a decade away from solar PV being cheaper per megawatt-hour than the fuel cost for a light water reactor. Better use of uranium ore and fission products could be critical to nuclear's competitiveness.
The non-proliferation lobby opposes any attempts to recycle fuel or make enriched fuel cheaper. The concern comes from the dual-use nature of these technologies. Instead of performance-based targets, it is just "No." If there is no compromise, nuclear will likely remain a small part of our energy use.
If we extend probabilistic thinking to fuel supplies, paths open up. It isn't ideal that we have plutonium-containing fuel that will be radioactive for hundreds of thousands of years spread throughout the world. And it isn't great that our only commercial recycling technology is the PUREX process designed to make weapons material. There are alternatives like pyroprocessing that don't generate pure plutonium. Some studies suggest that pyroprocessing might already be cheaper than PUREX. It drinks electricity like water. Costs could fall further with less expensive electricity, closing the gap with mined uranium. Adopting processes like these could eliminate stored plutonium and reduce fast reactor fuel costs without being useful as a weapons technology.
New Reactors Need Testing Slots
You need testing locations if iterative testing is the easiest way to navigate performance-based regulations. Federal sites making it hard for startups and other non-traditional customers to get slots is nothing new. SpaceX had to develop its engine testing center in McGregor, TX (the site was home to a failed rocket startup) instead of getting access to existing test stands at Stennis Space Center. When no traditional launch site would give them space, SpaceX had to go to the Kwajalein Atoll in the Pacific Ocean to launch Falcon 1. Once SpaceX broke through, things finally loosened up. Half a dozen startups have leases for launch pads at various NASA and Air Force facilities, and startups like Relativity Space test engines at Stennis.
The US only has one facility for megawatt-scale testing, Idaho National Lab (INL). If INL abuses this monopoly out of laziness or status seeking to the extent that potential users refer to going there as the "INL Tax," it could bottleneck the entire nuclear ecosystem.
Part of KRUSTY's development speed advantage is that they had their choice of test sites. More facilities can accommodate kilowatt scale tests. The team used existing equipment at the Nevada National Security Site with only minor regulatory exceptions.
Making national labs more user-friendly has nothing to do with the usual nuclear regulation complaints, but it is critical for the industry's success. Pragmatic startups may need to start small enough that they can find their own Kwajalein Atoll.
The Evolutionary Paths We Want
We will likely get at least a few small modular light water reactors. And our existing fleet could run many decades longer where electricity market conditions justify their continued operation. Subsidies will keep those plants operating longer but also reduce pressure to continue the modernization of regulations.
Agile firms that can rapidly test and build their designs will play a role in the megawatt-scale remote power generation market and possibly graduate to larger plants where the economics work.
Those are all good things, but much of the future lies with KRUSTY-like kilowatt-scale systems. Nuclear has a power density problem that keeps it from powering our cars and planes. The shielding and heat engines are too heavy. The radiation and particles are harmful because they contain a lot of energy. The answer is to make solid-state technologies that convert heat and radiation into electricity. It is theoretically possible to turn gamma rays into electricity with something similar to a solar cell. Shielding gets lighter and generates electricity! It also brings new life to many isotopes that require too much shielding to be practical in radioisotope generators. In the meantime, kilowatt-scale systems can compete in smaller remote power applications and supplement solar microgrids. Further cost decreases could enable electricity customers to defect from the grid where solar is not feasible. Competing manufacturers promise a much more competitive industry than exists today, where incentives rarely encourage falling prices.
The endgame is a chunk of nuclear material that can regulate itself based on user demand, surrounded by energy-capturing devices that soak up every bit of emitted energy. Power density could exceed today's liquid fuels and batteries while having extreme energy density. We'd finally get our flying cars! Reactors that look like KRUSTY are on the path to that endgame.