W. Edwards Deming and his Ideas
W. Edwards Deming was an American management thinker whose ideas were ignored by Americans until they were used by foreign automakers, namely Toyota, to pummel domestic automakers. Toyota Production System (TPS) and its imitator, Lean Manufacturing, are partly based on these principles.
The Challenges of Car Manufacturing
A Toyota Camry has roughly 30,000 parts and 70,000 individual processes. Toyota Camry is usually the highest quality car produced, where quality means the absence of defects. Camry can be as low as 70 defects per 100 cars using JD Power's methodology. Each part or process only has a defect one in 150,000 times.
Automotive manufacturing is competitive, low margin, capital intensive, and labor-intensive. It is an "O-ring" industry where one missing part shuts down a manufacturing line. Minimizing the cash used in CAPEX, labor, and working capital is key to survival. Survival is no joke. Out of thousands of American automobile companies that have existed, only Tesla and Ford have never declared bankruptcy. Auto manufacturers that minimize cash expenditure and run their factories at high utilization dominate over time.
Deming's Basic Principles for Quality
Deming touted his views on quality management as a "System of Profound Knowledge," from which he derived 14 principles. There is an entire cannon associated with these, which I will not cover. It may be surprising that quality is the gateway drug to minimizing cash usage across a giant organization.
Concepts in the 14 principles include:
-
Continuously improve processes.
-
Improve quality by improving the process, rather than using inspections.
It is expensive to fix or scrap something after building it. It is cheaper to improve the process so that it never produces defects in the first place. Quality is the gateway drug for minimizing cash usage.
-
Work with fewer suppliers. Choose suppliers that care about quality and provide the most value rather than always choosing the low bidder.
-
Improve processes in every part of the organization, avoiding local optimums.
-
Make sure people have the training and tools to do their jobs
-
Do not shoot the messenger. Improving processes requires reporting defects. Defects come from poorly designed processes, not employees.
-
Rely on process knowledge and clear communication instead of slogans, arbitrary quotas, numerical management targets, or rating systems.
There should be a definition of what a good part is. If good parts come out, then everyone can be proud. Managers should be spending most of their time on the floor to learn about the process and help improve it. If managers understand their plants, they know their capabilities. They can work with their teams without using targets that come with penalties.
Some of this may sound unworkable, but Toyota found ways to apply all these principles in practical ways. If you want to know more about this, I'd recommend reading "The Gold Mine" by Michael and Freddy Balle.
Creation of the Toyota Production System
Toyota leadership was already primed for these ideas and started to implement them. They submitted their progress and won a Deming Prize in 1965. Toyota doubled down on its progress after seeing results. They hashed out what we know today as Toyota Production System through continuous improvement.
Interesting concepts emerge in applying the 14 principles:
-
Anything a customer does not value is waste. Toyota details eight common types.
-
Inventory is one type of waste, and the most famous.
Controlling inventory is a proxy for understanding the process and understanding variability within the process. Trying to reduce inventory without understanding usually leads to line shutdowns because of missing parts. Excess inventory also has numerous direct costs and negatively impacts quality.
-
Aspire to reduce the number of parts and processes
The simpler the production system, the easier it is to produce products without defects.
-
Robots should be avoided if possible, especially in general assembly, because factory utilization is critical.
Robots are inflexible. They are expensive to buy and maintain. If you have thousands of robots, it tends to limit how many models you can make on one line and how fast you can update models. You end up with expensive, underutilized robots when consumer demand changes.
Robots are a local optimizer's love language. A redesign or change of assumptions is often more appropriate.
Robots are tools, not magic.
America Imitates
Japanese culture has a strong respect for quality. Using quality as the gateway drug for process improvements resonates. Even today, Toyota gets better results from their Japanese factories than their foreign factories.
After Detroit started losing market share, they realized they needed to adopt some of these principles to survive. The result has been a half-hearted acceptance and an absolute atrocity in vocabulary. Using the Japanese terms can get lost in translation, but the American adoptions are even worse. It may be only a slight exaggeration to hear something like:
Lean Enthusiast: I am a Lean Six-Sigma Black Belt Kaizen Sensai DMAIC TOC TPM 5S Kanban Poka-yoke Muda specialist! Let us go to the Gemba so I can help you, Detroit Autoworker!
Detroit Autoworker: Excuse me, sir, I work 40 hours a week for a livin', just to send it on down the line.
Even though Toyota Production System and Lean have produced results, only half of the Fortune 500 uses Lean. The number is likely to be drastically lower for total US companies. The US industry that is most committed to Lean is the software industry. TPS and Deming's principles were reimagined and adapted as Agile Software Development, which most software companies use in some form (Even parts of the government use it!).
America Does Deming Its Way
America's manufacturing industry has never owned Deming's principles by turning it into a coherent ideology, but that may be changing. Tesla Motors has made an unheralded (compared to its media attention) turnaround by adopting or independently discovering Deming's ideas. If I had to use a word to describe this new thinking, I would use METAL. Just for fun, I will use METAL Manufacturing to describe this new take on Lean.
The Unlikely Leader
Tesla and its CEO Elon Musk did not appear likely candidates for a Toyota-like epiphany. While Tesla has always been detail-oriented in delivering a product that customers love, they were less focused on manufacturing. Tesla had a rocky start manufacturing its first mass-market car, the Model 3, in 2017. Musk and Tesla were committed to building the first version of a fully automated factory, known as the Alien Dreadnaught, that would eventually have robot arms moving so fast that air friction would be a design factor. High-speed robots would maximize the velocity and density of the manufacturing line. Musk bristled at any comparison of Tesla and Toyota.
As we now know, this automation drive was over-ambitious. Some learning from the infamous Fluffer Bot in late 2017:
Elon Musk: One example would be, we have this – this is sort of ironically foolish – we had these fiberglass mats on the top of the battery pack. They're basically fluff. So, we tried to automate the placement and bonding of fluff to the top of the battery pack, which is ridiculous. So, we had fluffer bot, which was really an incredibly difficult machine to make work. Machines are not good at picking up pieces of fluff. Human hands are way better at doing that. And so, we had a super complicated machine using a vision system to try to put a piece of fluff on the battery pack.
One of the questions I asked was, do we actually need that? So, we tested a car with and without and found out that there was no change in the noise volume in the cabin. So, we actually had a part that was unnecessary. That was forced – line kept breaking down because fluffer bot would frequently just failed to pick up the fluff while put it in, like, a random location. So that was one of the silliest things I found.
Tesla learns fast. In the summer of 2018, the Model 3 production ramp stalled. The culprit was their highly automated general assembly line. In a classic Lean case study, Tesla used discarded conveyor belts and built a new assembly line in a structured tent in only three weeks. Almost right from the start, the tent line with minimal robots had similar labor hours and defect rates per car as the robot line.
Then came the final proof that Tesla was adopting these principles in Q2 2019. There is a "Lean Turnaround" niche in the business novel book category. At the end of these books, the factory manager and the mentor admire the warehouse that went from piles of parts inventory to practically empty. Here we go:
Jerome Guillen (President of Automotive): Yes. We are improving the material delivery for S and X just like we have done for Model 3 of some ready components. We reduced production part warehousing costs by again 90%, 9-0, since Q3 last year and so we're making a lot of room. We have - we're much more efficient with parts delivery.
It helps that increasing production actually. So that’s space that we cleared out, I'm looking at it right now in Fremont, which is going to put Model Y stuff in there. So every -- if you visit the factory from, I would say, every six months you'd have a hard time recognizing and finding their way. Yeah. It's constantly changing and evolving.
90%, 9-0 reduction in parts inventory cost in 6 months. Tesla had vastly improved knowledge and control of its process, shown by massive inventory improvements that did not cause line shutdowns. And the extra space meant the new SUV, Model Y, would not need a new factory. Proponents of Toyota and Lean were right that Tesla would have to change to survive.
Bigger, Better, Faster
Tesla would not be METAL if it just copied basic Lean ideas. Instead of incremental changes to make a process more efficient using existing methods, Tesla started developing new technologies to jump a level above Lean and apply these ideas across the entire value chain. These statements define how Tesla attacks with METAL:
- Use First Principles - explore all the possibilities that physics allows
- The Best Part is No Part
- The Best Service is No Service
Let's see how a METAL enthusiast and Fremont Autoworker interact:
METAL enthusiast: What frustrates you, Fremont Autoworker?
Fremont Autoworker: Sandy Munro keeps making fun of us for our Model 3 body. It has more parts and is more over-designed than any other automaker! What should we do?
METAL enthusiast: The die-cast toy Model S in the gift shop is only one piece. NO PART IS THE BEST PART.
Fremont Autoworker: Right, but die-cast aluminum parts are limited for structural components because they have to be heat-treated for strength, warping the casting. And I just did the math, if we broke the underbody into a few parts it would require bigger casting machines than exist today.
METAL enthusiast: Think of FIRST PRINCIPLES, you must!
Fremont Autoworker: Ok, Ok. I'll get the materials science team to invent a new aluminum alloy that can be cast and is strong enough to eliminate the heat treat. And I better call the Italians and tell them to start building the biggest casting machines in the world. We will eliminate hundreds of parts and hundreds of robots in the factory!
METAL enthusiast: Call it GIGAPRESS!
Other METAL highlights:
-
Tesla has eliminated radars, rain sensors, instrument panels, and buttons from their cars through software.
Tesla's computer vision software replaced radar and IR rain sensors in the cars. The radars used for driver assistance cost $100-$200 per car, which adds up fast. Cost savings and revenue from selling Autopilot software pay for the development of the autonomous driving software. Rather than a defined customer launch, Tesla improves its driving software over time, adding features as they are ready. It doesn't get more METAL than conserving cash by developing new technology. Most competitors are either not investing in the technology or incinerating billions of dollars in development programs that have never seen a customer.
-
Customers order online instead of buying from dealers
Online orders started as a customer-focused improvement. TPS has demand-pull production instead of production-push. In its factories, it uses "Kanban" cards. A station starts its job when it receives a card signifying the process needs its part. The cards keep the factory in sync. In online orders and pre-orders, Tesla has a system of digital "Kanban" cards that spans its entire value chain. Unsold inventory at Tesla dealerships is close to zero. Toyota has around 30 days of inventory (parts, work-in-progress, and finished product) in its manufacturing system. It offloads cars to dealerships, where there is usually about 45 days of inventory on lots. Toyota has 75 days in its entire value chain. Tesla's days of inventory include vehicles in transit to customers and unsold cars. It was most recently 43 days. Because Tesla clusters deliveries at the end of the quarter, it is hard to tell how representative this number is. Under 20 days is the target once factories come online in the three major markets, allowing a reduction of cars in transit.
-
Cybertruck
Cybertruck has a stainless steel exoskeleton made from bending plates of steel like origami. It saves hundreds of millions in tooling and paint shop CAPEX, reduces part count, reduces weight, and is more durable. The exterior is bare metal. No paint is required.
-
Eliminate parts customers aren't using
The passenger seat lumbar support system got deleted since the software showed no one used it.
-
Reducing maintenance
After issues with older Model S drive units, Tesla set out to design its powertrains to last 1 million miles. More reliable vehicles reduce CAPEX and OPEX by reducing the need for service centers and service employees.
-
No Model Years
Upgrades happen as they are available instead of being clustered in model years. There is continuous improvement instead of discontinuous improvement.
-
Software is the process
Lean and TPS are analog processes at heart. A typical bogeyman in Lean turnarounds is the software-loving materials ordering employee that causes waves of instability in the process with naive ordering practices. Cards, tags, and paper are preferred.
METAL manufacturing is digital. Tesla writes and constantly improves its custom operating system that assists in running the company. Sales can talk to materials, each car carries records of its journey through the manufacturing process, etc. Software can be an evil materials ordering system or something useful.
As more of the process becomes code, the code becomes the process. Describing the process to a computer in 1s and 0s requires precision that would make any Lean practitioner proud. The base machine code can be abstracted into human-readable code, making the code the process documentation. Having more process knowledge in code also makes it easier to open new facilities. Analog processes have more of their know-how embedded in humans, making transfer difficult. Writing software like this is a real challenge but pays dividends. Using Lean principles in the software development process makes it possible.
-
Software Widens the Design Space
One criticism of TPS and Lean organizations is that they struggle to apply their principles to departments outside of manufacturing. Some of the worst offenders are product development and research. "Go and See" and other Lean tools break down when the entire process is in a human brain. METAL Manufacturing solves this by finding curious engineers, giving them the best modeling software and hardware stack money can buy or build, ratcheting up their ambition, and letting them sink their teeth into a problem with only the laws of physics as their constraints. Engineers get vasty more iterations exploring designs, leading to superior outcomes at drastically lower cost. Tesla has standard setting designs for cooling systems, heat pumps, electronics packaging, battery packs, and electric motors, to name a few categories. You can see the nitty-gritty details for yourself on Sandy Munro's Youtube channel.
To fuel all this, Tesla hoovers up massive amounts of talent. METAL manufacturing requires talented engineers. Talented engineers love the ambition and freedom of METAL.
Musk may one day get his Alien Dreadnaught, but it will probably look more like a few giant machines spitting out big chunks of the car, a few robots putting those pieces together, then the equivalent of a NASCAR pit crew snapping in modules. This dreadnaught would have many times the value velocity and density of a factory full of blazing-fast robots.
Numerical Comparison
I'm posting raw numbers because there are many ways to compare a growing automaker to mature automakers.
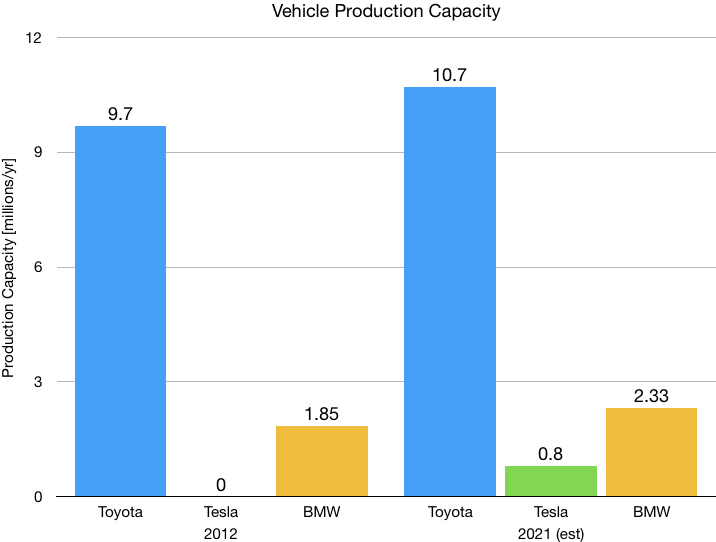
Tesla experienced a 47% CAGR from 2013 to 2020. It plans to continue to grow at a similar rate.
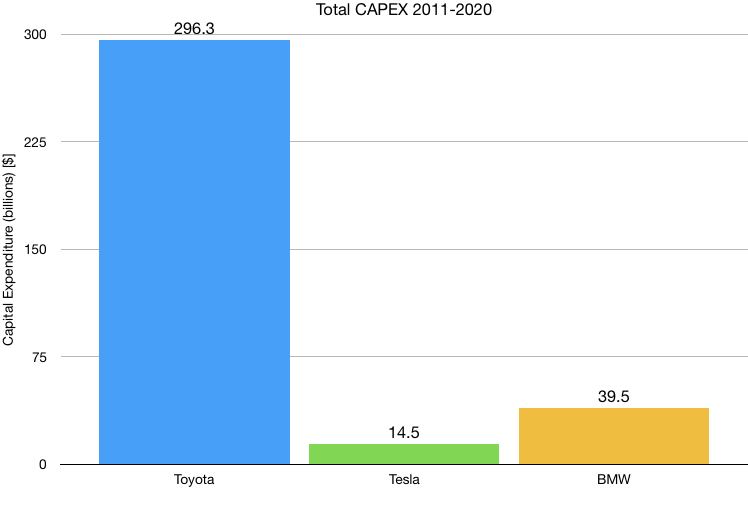
Tesla CAPEX includes a global supercharger network, dealerships, and service centers. It also includes sub-assemblies like seat manufacturing that other automakers do not have in house.
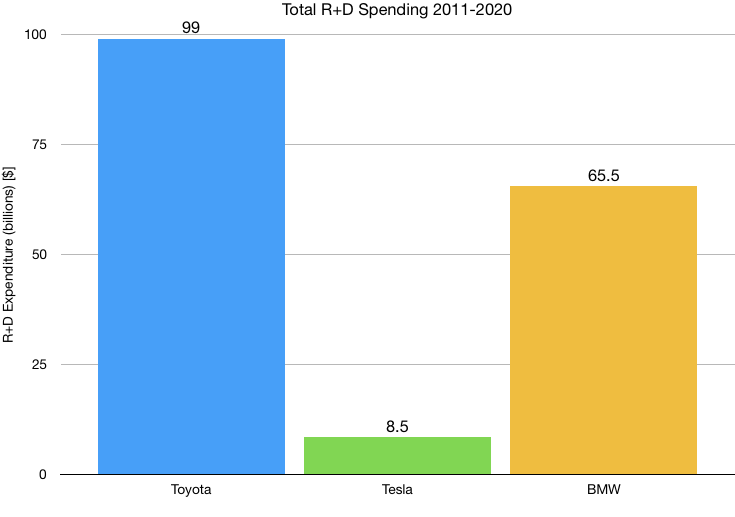
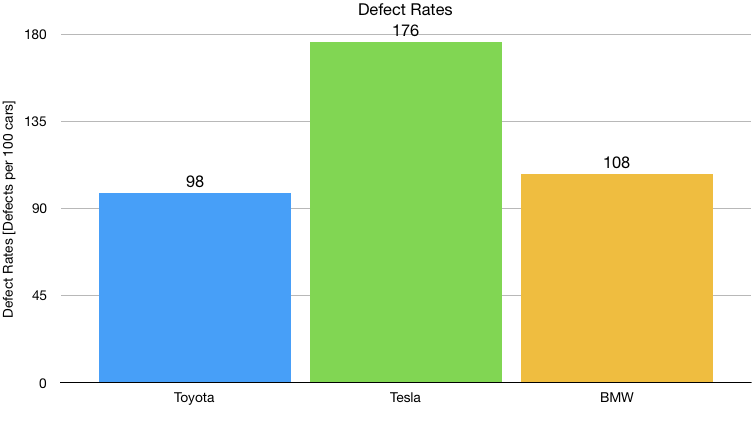
Toyota cars are estimated to have 3x the parts and processes than Tesla, meaning the gap in defects per part is much larger than appears. METAL enthusiasts aggressively reduce part count because trying to beat Toyota at its own game is tough. METAL Manufacturing excels in other areas to level the playing field while continuous improvement decreases defects per part. Tesla's defects are mainly in paint, fit, and finish, while the powertrains have become very reliable.
Also note that this is the Toyota brand, Lexus is Toyota owned and has a score of 80. Lexus is probably more comparable to BMW and Tesla.
The Coming Realignment
For those keeping score at home, a CEO of a competing auto manufacturer has to:
-
Figure out how to reform their dealership network so they can reduce overhead and inventory.
-
Close somewhere between 50% and 80% of their factories as electrification, software, and other technologies reduce the number of parts and processes in car manufacturing.
-
Learn how to be as good at software as they are at logistics and manufacturing.
Designing electric cars is the easy part.
Before you buy Tesla stock because of METAL Manufacturing, consider that this is car manufacturing. Things can go wrong. Companies run by METAL enthusiasts will likely emerge in China and India. The bull case is that Tesla uses manufacturing technology as a moat to grow an install base, then sells high margin services (insurance, software) to this install base. The bear case is bankruptcy.
There is another industry where METAL enthusiasts have created dozens of new companies. And they will probably have more impact on our lives than a better car. In a follow-up post, I will cover the aerospace industry going METAL.
Disclosure: This is not investment advice. I bought Tesla stock in 2014 to justify all the time I spent reading Tesla 10-Ks, 10-Qs, and conference call transcripts. I have not sold any stock, because I do not want to lose my justification.
How to Build a Giant Carmaker
2021 June 30 Twitter Substack See all postsAmerica finally owns Deming, and a manufacturing renaissance may follow
W. Edwards Deming and his Ideas
W. Edwards Deming was an American management thinker whose ideas were ignored by Americans until they were used by foreign automakers, namely Toyota, to pummel domestic automakers. Toyota Production System (TPS) and its imitator, Lean Manufacturing, are partly based on these principles.
The Challenges of Car Manufacturing
A Toyota Camry has roughly 30,000 parts and 70,000 individual processes. Toyota Camry is usually the highest quality car produced, where quality means the absence of defects. Camry can be as low as 70 defects per 100 cars using JD Power's methodology. Each part or process only has a defect one in 150,000 times.
Automotive manufacturing is competitive, low margin, capital intensive, and labor-intensive. It is an "O-ring" industry where one missing part shuts down a manufacturing line. Minimizing the cash used in CAPEX, labor, and working capital is key to survival. Survival is no joke. Out of thousands of American automobile companies that have existed, only Tesla and Ford have never declared bankruptcy. Auto manufacturers that minimize cash expenditure and run their factories at high utilization dominate over time.
Deming's Basic Principles for Quality
Deming touted his views on quality management as a "System of Profound Knowledge," from which he derived 14 principles. There is an entire cannon associated with these, which I will not cover. It may be surprising that quality is the gateway drug to minimizing cash usage across a giant organization.
Concepts in the 14 principles include:
Continuously improve processes.
Improve quality by improving the process, rather than using inspections.
It is expensive to fix or scrap something after building it. It is cheaper to improve the process so that it never produces defects in the first place. Quality is the gateway drug for minimizing cash usage.
Work with fewer suppliers. Choose suppliers that care about quality and provide the most value rather than always choosing the low bidder.
Improve processes in every part of the organization, avoiding local optimums.
Make sure people have the training and tools to do their jobs
Do not shoot the messenger. Improving processes requires reporting defects. Defects come from poorly designed processes, not employees.
Rely on process knowledge and clear communication instead of slogans, arbitrary quotas, numerical management targets, or rating systems.
There should be a definition of what a good part is. If good parts come out, then everyone can be proud. Managers should be spending most of their time on the floor to learn about the process and help improve it. If managers understand their plants, they know their capabilities. They can work with their teams without using targets that come with penalties.
Some of this may sound unworkable, but Toyota found ways to apply all these principles in practical ways. If you want to know more about this, I'd recommend reading "The Gold Mine" by Michael and Freddy Balle.
Creation of the Toyota Production System
Toyota leadership was already primed for these ideas and started to implement them. They submitted their progress and won a Deming Prize in 1965. Toyota doubled down on its progress after seeing results. They hashed out what we know today as Toyota Production System through continuous improvement.
Interesting concepts emerge in applying the 14 principles:
Anything a customer does not value is waste. Toyota details eight common types.
Inventory is one type of waste, and the most famous.
Controlling inventory is a proxy for understanding the process and understanding variability within the process. Trying to reduce inventory without understanding usually leads to line shutdowns because of missing parts. Excess inventory also has numerous direct costs and negatively impacts quality.
Aspire to reduce the number of parts and processes
The simpler the production system, the easier it is to produce products without defects.
Robots should be avoided if possible, especially in general assembly, because factory utilization is critical.
Robots are inflexible. They are expensive to buy and maintain. If you have thousands of robots, it tends to limit how many models you can make on one line and how fast you can update models. You end up with expensive, underutilized robots when consumer demand changes.
Robots are a local optimizer's love language. A redesign or change of assumptions is often more appropriate.
Robots are tools, not magic.
America Imitates
Japanese culture has a strong respect for quality. Using quality as the gateway drug for process improvements resonates. Even today, Toyota gets better results from their Japanese factories than their foreign factories.
After Detroit started losing market share, they realized they needed to adopt some of these principles to survive. The result has been a half-hearted acceptance and an absolute atrocity in vocabulary. Using the Japanese terms can get lost in translation, but the American adoptions are even worse. It may be only a slight exaggeration to hear something like:
Even though Toyota Production System and Lean have produced results, only half of the Fortune 500 uses Lean. The number is likely to be drastically lower for total US companies. The US industry that is most committed to Lean is the software industry. TPS and Deming's principles were reimagined and adapted as Agile Software Development, which most software companies use in some form (Even parts of the government use it!).
America Does Deming Its Way
America's manufacturing industry has never owned Deming's principles by turning it into a coherent ideology, but that may be changing. Tesla Motors has made an unheralded (compared to its media attention) turnaround by adopting or independently discovering Deming's ideas. If I had to use a word to describe this new thinking, I would use METAL. Just for fun, I will use METAL Manufacturing to describe this new take on Lean.
The Unlikely Leader
Tesla and its CEO Elon Musk did not appear likely candidates for a Toyota-like epiphany. While Tesla has always been detail-oriented in delivering a product that customers love, they were less focused on manufacturing. Tesla had a rocky start manufacturing its first mass-market car, the Model 3, in 2017. Musk and Tesla were committed to building the first version of a fully automated factory, known as the Alien Dreadnaught, that would eventually have robot arms moving so fast that air friction would be a design factor. High-speed robots would maximize the velocity and density of the manufacturing line. Musk bristled at any comparison of Tesla and Toyota.
As we now know, this automation drive was over-ambitious. Some learning from the infamous Fluffer Bot in late 2017:
Tesla learns fast. In the summer of 2018, the Model 3 production ramp stalled. The culprit was their highly automated general assembly line. In a classic Lean case study, Tesla used discarded conveyor belts and built a new assembly line in a structured tent in only three weeks. Almost right from the start, the tent line with minimal robots had similar labor hours and defect rates per car as the robot line.
Then came the final proof that Tesla was adopting these principles in Q2 2019. There is a "Lean Turnaround" niche in the business novel book category. At the end of these books, the factory manager and the mentor admire the warehouse that went from piles of parts inventory to practically empty. Here we go:
90%, 9-0 reduction in parts inventory cost in 6 months. Tesla had vastly improved knowledge and control of its process, shown by massive inventory improvements that did not cause line shutdowns. And the extra space meant the new SUV, Model Y, would not need a new factory. Proponents of Toyota and Lean were right that Tesla would have to change to survive.
Bigger, Better, Faster
Tesla would not be METAL if it just copied basic Lean ideas. Instead of incremental changes to make a process more efficient using existing methods, Tesla started developing new technologies to jump a level above Lean and apply these ideas across the entire value chain. These statements define how Tesla attacks with METAL:
Let's see how a METAL enthusiast and Fremont Autoworker interact:
Other METAL highlights:
Tesla has eliminated radars, rain sensors, instrument panels, and buttons from their cars through software.
Tesla's computer vision software replaced radar and IR rain sensors in the cars. The radars used for driver assistance cost $100-$200 per car, which adds up fast. Cost savings and revenue from selling Autopilot software pay for the development of the autonomous driving software. Rather than a defined customer launch, Tesla improves its driving software over time, adding features as they are ready. It doesn't get more METAL than conserving cash by developing new technology. Most competitors are either not investing in the technology or incinerating billions of dollars in development programs that have never seen a customer.
Customers order online instead of buying from dealers
Online orders started as a customer-focused improvement. TPS has demand-pull production instead of production-push. In its factories, it uses "Kanban" cards. A station starts its job when it receives a card signifying the process needs its part. The cards keep the factory in sync. In online orders and pre-orders, Tesla has a system of digital "Kanban" cards that spans its entire value chain. Unsold inventory at Tesla dealerships is close to zero. Toyota has around 30 days of inventory (parts, work-in-progress, and finished product) in its manufacturing system. It offloads cars to dealerships, where there is usually about 45 days of inventory on lots. Toyota has 75 days in its entire value chain. Tesla's days of inventory include vehicles in transit to customers and unsold cars. It was most recently 43 days. Because Tesla clusters deliveries at the end of the quarter, it is hard to tell how representative this number is. Under 20 days is the target once factories come online in the three major markets, allowing a reduction of cars in transit.
Cybertruck
Cybertruck has a stainless steel exoskeleton made from bending plates of steel like origami. It saves hundreds of millions in tooling and paint shop CAPEX, reduces part count, reduces weight, and is more durable. The exterior is bare metal. No paint is required.
Eliminate parts customers aren't using
The passenger seat lumbar support system got deleted since the software showed no one used it.
Reducing maintenance
After issues with older Model S drive units, Tesla set out to design its powertrains to last 1 million miles. More reliable vehicles reduce CAPEX and OPEX by reducing the need for service centers and service employees.
No Model Years
Upgrades happen as they are available instead of being clustered in model years. There is continuous improvement instead of discontinuous improvement.
Software is the process
Lean and TPS are analog processes at heart. A typical bogeyman in Lean turnarounds is the software-loving materials ordering employee that causes waves of instability in the process with naive ordering practices. Cards, tags, and paper are preferred.
METAL manufacturing is digital. Tesla writes and constantly improves its custom operating system that assists in running the company. Sales can talk to materials, each car carries records of its journey through the manufacturing process, etc. Software can be an evil materials ordering system or something useful.
As more of the process becomes code, the code becomes the process. Describing the process to a computer in 1s and 0s requires precision that would make any Lean practitioner proud. The base machine code can be abstracted into human-readable code, making the code the process documentation. Having more process knowledge in code also makes it easier to open new facilities. Analog processes have more of their know-how embedded in humans, making transfer difficult. Writing software like this is a real challenge but pays dividends. Using Lean principles in the software development process makes it possible.
Software Widens the Design Space
One criticism of TPS and Lean organizations is that they struggle to apply their principles to departments outside of manufacturing. Some of the worst offenders are product development and research. "Go and See" and other Lean tools break down when the entire process is in a human brain. METAL Manufacturing solves this by finding curious engineers, giving them the best modeling software and hardware stack money can buy or build, ratcheting up their ambition, and letting them sink their teeth into a problem with only the laws of physics as their constraints. Engineers get vasty more iterations exploring designs, leading to superior outcomes at drastically lower cost. Tesla has standard setting designs for cooling systems, heat pumps, electronics packaging, battery packs, and electric motors, to name a few categories. You can see the nitty-gritty details for yourself on Sandy Munro's Youtube channel.
To fuel all this, Tesla hoovers up massive amounts of talent. METAL manufacturing requires talented engineers. Talented engineers love the ambition and freedom of METAL.
Musk may one day get his Alien Dreadnaught, but it will probably look more like a few giant machines spitting out big chunks of the car, a few robots putting those pieces together, then the equivalent of a NASCAR pit crew snapping in modules. This dreadnaught would have many times the value velocity and density of a factory full of blazing-fast robots.
Numerical Comparison
I'm posting raw numbers because there are many ways to compare a growing automaker to mature automakers.
Tesla experienced a 47% CAGR from 2013 to 2020. It plans to continue to grow at a similar rate.
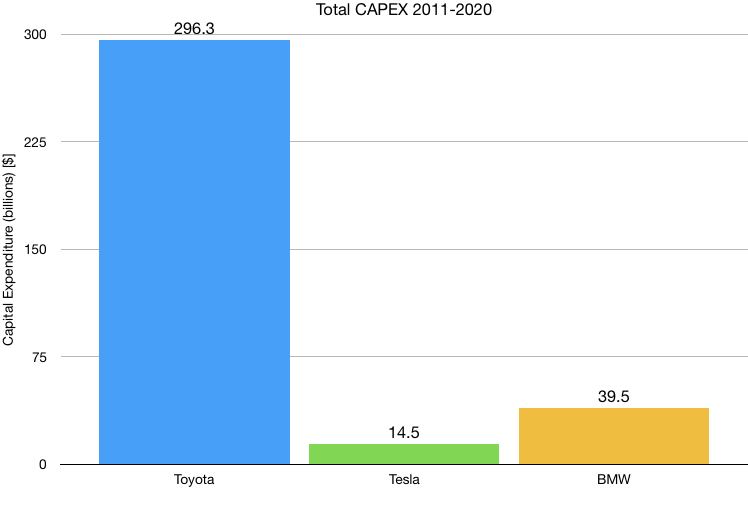
Tesla CAPEX includes a global supercharger network, dealerships, and service centers. It also includes sub-assemblies like seat manufacturing that other automakers do not have in house.
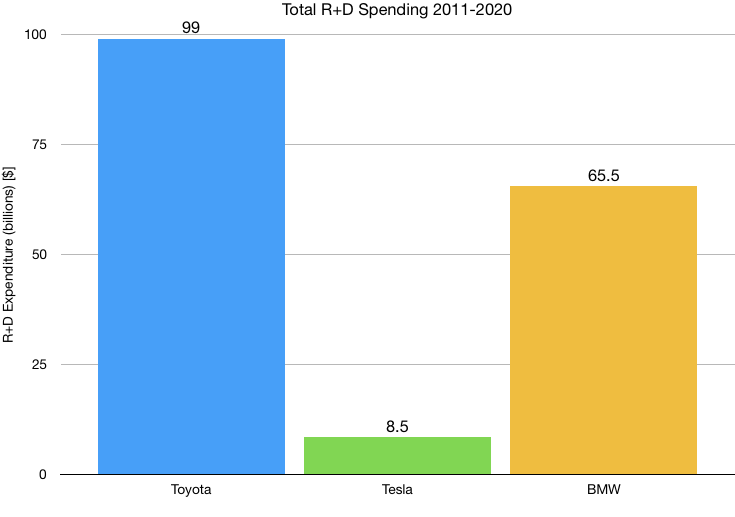
Toyota cars are estimated to have 3x the parts and processes than Tesla, meaning the gap in defects per part is much larger than appears. METAL enthusiasts aggressively reduce part count because trying to beat Toyota at its own game is tough. METAL Manufacturing excels in other areas to level the playing field while continuous improvement decreases defects per part. Tesla's defects are mainly in paint, fit, and finish, while the powertrains have become very reliable.
Also note that this is the Toyota brand, Lexus is Toyota owned and has a score of 80. Lexus is probably more comparable to BMW and Tesla.
The Coming Realignment
For those keeping score at home, a CEO of a competing auto manufacturer has to:
Figure out how to reform their dealership network so they can reduce overhead and inventory.
Close somewhere between 50% and 80% of their factories as electrification, software, and other technologies reduce the number of parts and processes in car manufacturing.
Learn how to be as good at software as they are at logistics and manufacturing.
Designing electric cars is the easy part.
Before you buy Tesla stock because of METAL Manufacturing, consider that this is car manufacturing. Things can go wrong. Companies run by METAL enthusiasts will likely emerge in China and India. The bull case is that Tesla uses manufacturing technology as a moat to grow an install base, then sells high margin services (insurance, software) to this install base. The bear case is bankruptcy.
There is another industry where METAL enthusiasts have created dozens of new companies. And they will probably have more impact on our lives than a better car. In a follow-up post, I will cover the aerospace industry going METAL.
Disclosure: This is not investment advice. I bought Tesla stock in 2014 to justify all the time I spent reading Tesla 10-Ks, 10-Qs, and conference call transcripts. I have not sold any stock, because I do not want to lose my justification.