Battery-Powered Ship Basics
The Challenges
Most climate analysts consider cargo ships hard to decarbonize. I think this is for several reasons:
-
The popular battery chemistries have excellent power density to accelerate cars or regulate electricity grid frequency. They need constant use to recoup their high cost. Batteries that can discharge in a few hours are massive overkill when ships might prefer to go one week or more without charging.
-
People calculate how many batteries it takes to replace all the fuel cargo ships carry or assume an extreme trip length.
-
It would take too long to charge or fast charging a ship dockside would have a horrific power draw.
Ships are great at carrying bulky and heavy stuff with minimal cost and energy usage. We need a battery chemistry that leans into that and sacrifices performance to reduce cost. Electrification also requires a different business model for charging the batteries.
Checking the Math
Let's examine powering a 10,000 TEU container ship from New York to Rotterdam with the cheapest volume battery chemistry we have, lithium iron phosphate (LFP). At the max continuous speed of 22 knots, power usage is ~40 MW. The trip distance is 3800 miles, so we need ~150 hours of power or 6 GWh. These ships carry ~2 million gallons of fuel, which equates to ~7.5 million liters. The latest CATL Qilin LFP packs contain 290 Wh/l. We can fit nearly 2.2 GWh just in our fuel storage space. Two-stroke marine diesel engines are massive, and we can get another ~0.5 GWh from reducing engine room space and ballast. The last 3.6 GWh can fit in less than 450 TEUs. So we can cross oceans losing only 4.5% of cargo space while gaining the benefits of electrification. The mass performance is not as good, with the batteries using 25% of the cargo mass after netting out fuel and engines. Ships carrying lighter containers would see little cargo penalty, but those carrying heavier goods would.
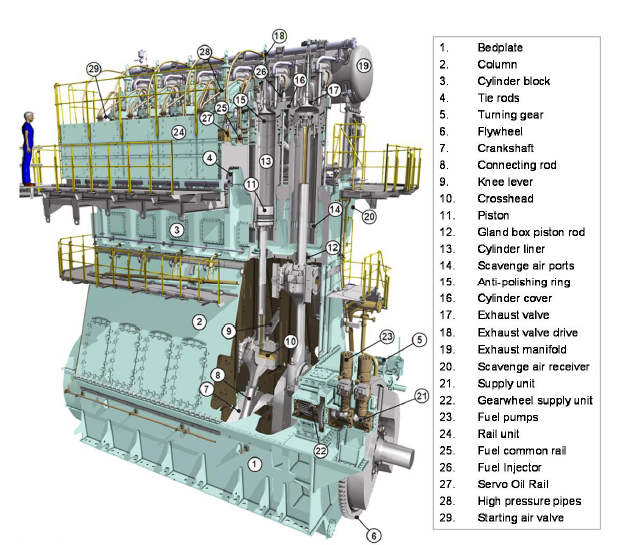
They get way bigger than this! Source
The startup Fleet Zero has a solution for the charging problem - containerize the batteries, charge them nearby the port, and load them like regular cargo. Ships carry so much fuel today because few fuel sales points offer the required scale, quality, and cost. Filling up at the best places and using large fuel tanks is the way to minimize cost. Recharging at each port will be the lowest cost strategy if batteries and electricity are cheaper than fuel, even if there is variation in prices between ports.
The issue with using LFP batteries is cost. 6 GWh of LFP batteries would cost over $600 million. The cost per cycle would be $110/MWh plus charging costs that could be anywhere from $30/MWh to $100/MWh. Heavy fuel oil at $80/barrel in a 45% efficient engine equates to ~$110/MWh. Business models like Fleet Zero assume multiple stops on routes (which cargo ships commonly do, anyway) and slower speeds. Ships carry fewer batteries on each leg, and the system requires fewer batteries. Cost per cycle drops to reasonable levels while cargo penalties decrease. But it would make adoption easier if cheaper batteries allowed ships to carry more batteries or increased their savings.
These numbers contrast with calculations from analysts like Vaclav Smil because he assumes a 30+ day non-stop trip from Asia to Europe. But shipping companies are in the business of making money, not non-stop voyages. They will stop a few times to swap batteries if it increases profitability.
Iron-Air Batteries to the Rescue?
Iron-Air Fundamentals
Iron-air batteries charge by turning rust into iron, releasing oxygen while absorbing electrons. They do the reverse to provide power. Their theoretical energy density is higher than today's batteries because they can get oxygen from the air instead of carrying it around in another material. The systems and conditions needed to make the batteries work lower their energy density close to mass market batteries, though that will likely improve with further iteration. A sometimes important feature for ships is that iron-air battery volumetric energy density (Wh/l) is much better than its specific energy (Wh/kg), helping vessels that might be space limited.
The battery models coming to market discharge in 100-150 hours, meaning ships will carry enough batteries for at least 4-6 days of travel.
Researchers studied iron-air batteries for cars in the 1970s. Getting them to work at high power densities and with enough cycles was challenging. Entrepreneurs have recently resurrected the technology for low-power applications like multi-day electricity storage. Research on the critical air-breathing cathode restarted in the mid-2000s, and the maturation of that technology led to the startup Form Energy breaking ground on a 50 gigawatt-hour-per-year factory in West Virginia in early 2023.
Other battery chemistries might fit better, but the iron-air chemistry is the only one with a gigawatt scale factory under construction.[1]
The Cargo Ship Use Case
Iron-air chemistry's best features for ships are its low cost, acceptable volumetric energy density, and low fire risk. The current manufacturing cost is likely between $20/kWh and $50/kWh. Form Energy's goal is $20/kWh, and the active material is only $6/kWh. The battery industry has been ruthless at eliminating non-active material from other chemistries. Prices might creep toward $10/kWh at scale. Energy density could be anywhere from 200 Wh/l to 1000 Wh/l based on historical research results. Iron-air batteries can't undergo thermal runaway like lithium-ion batteries, an advantage for ships where fire is a concern.
The negatives of iron-air batteries are low power density, limited cycle life, and poor charge efficiency. Power density isn't a big deal to ships because they want to use energy steadily rather than expending it in short bursts. Lower cycle life is manageable because batteries meant to discharge for days use fewer cycles. If a battery only does 40 cycles per year, 800 is a twenty-year supply! Thousands of uses are overkill. Iron-air batteries could also be amenable to inexpensive "refurbishment" rather than wholesale replacement. Charge efficiency is poor compared to lithium-ion batteries - only 60%. But losing some cheaper electricity is acceptable when competing with expensive liquid fuels.
Improving Ship Efficiency
Engineers almost always find ways to improve efficiency when designing electric vehicles. Better efficiency can improve range or reduce battery pack size besides cutting energy costs. Ships lose most energy through waste heat, propeller loss, and hull friction. Electric motors are much more efficient than marine engines, so the focus is on propellers and hull friction.
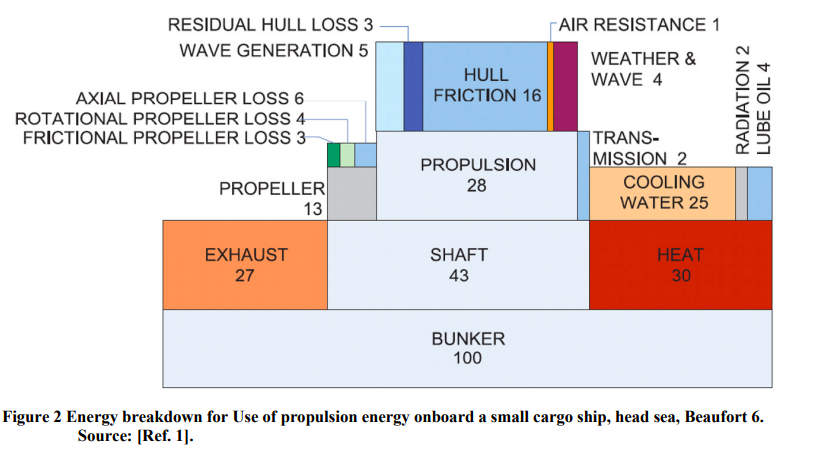
Hulls, propellers, and engines bleed energy. Source
There are many low-risk opportunities:
-
More Efficient Hull Forms
Optimized hull designs can be up to 20% more efficient than traditional ones. A 2016 report cites barriers to adoption as more upfront design time and coordination with shipyards. There will be more design and coordination effort when designing early battery-electric ships, so a better hull form should be a relatively easy bolt-on.
-
Better Hull Coatings
Anti-fouling coatings can reduce fuel usage by ~3% and will likely be more valuable to a battery electric ship than an oil-fueled one because of range extension.
-
Optimal Propeller Design and Conditioning
Ships can reduce fuel usage by 15%-20% by using more efficient propellers and improving the water flow conditions around them.
Large cargo ships almost all use giant two-stroke marine engines because they are efficient and reliable. Another advantage of two-stroke engines is that their slower-than-normal speed means they can directly drive propellers without expensive and complicated gears. That speed and location are not optimal for propeller efficiency, though.
Electric ships can use larger propellers with lower RPMs that are more efficient. They can also place the propellers further outside the wake using propulsion pods because electric motors are tiny compared to marine engines. Many cruise ships already use these because diesel-electric powertrains better match their requirements than direct-drive powertrains.
Fins and other devices can smooth the flow around the pods, further improving propeller efficiency.
-
Wider Efficiency Curves
The flexibility of electric powertrains can provide another 5%-10% reduction in fuel usage. Engines have a very narrow range where they operate at peak efficiency. In the real world, they rarely run in optimal conditions. Electric motors have good efficiency across a wide range of speeds.
-
Slow Steaming
Ships usually slow down when fuel costs are high because reducing speed can cut fuel consumption dramatically. A problem for ships with marine diesel engines is that engine efficiency drops precipitously at lower RPMs, resulting in diminishing returns for slow steaming. Electric motors don't share this issue, so they get the full benefits of slower travel. An electric ship will use ~1/8th of the power and ~1/4th of the energy to complete a trip if it halves its speed. Ship owners gain the ability to load up the batteries and blaze ahead if spot freight prices are high, or they can slow down to extend range and reduce costs if necessary. It is challenging to have both options with traditional cargo ships.
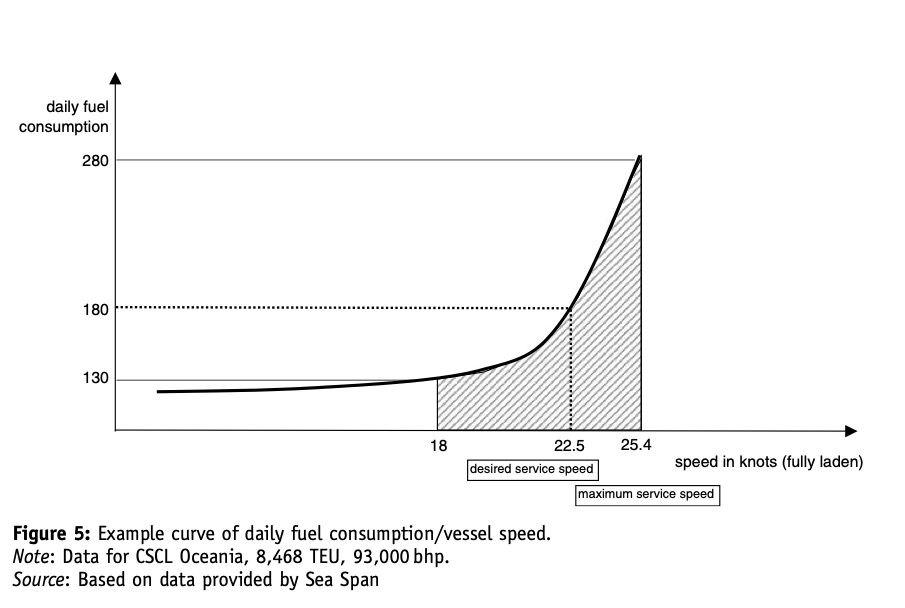
Reducing speed has diminishing returns for fuel consumption. Source
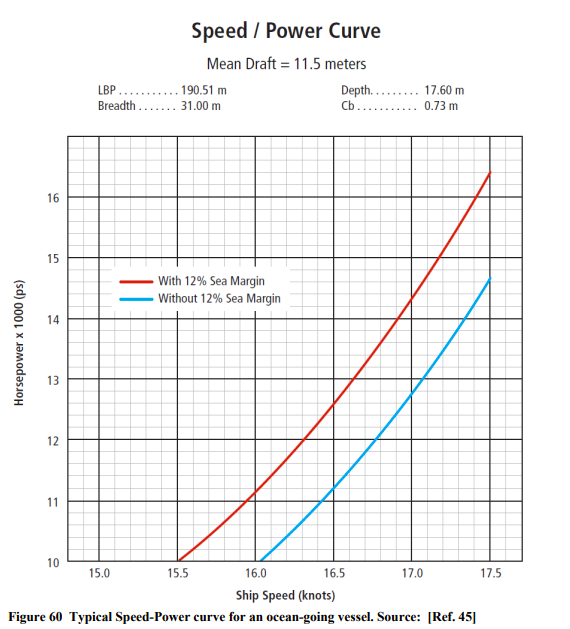
But only because of decreasing efficiency, delivered power still falls dramatically. Source
-
Other Operational Improvements
Accounting for weather in navigation plans, adjusting speed to allow for on-time arrivals, and optimizing trim and draft can cut fuel usage by ~8%. These will be more valuable to battery electric ships and might be easier to implement with electric powertrains.
Battery requirements should decrease by 25%-50% without losing any performance. There is an opportunity to reduce energy usage by 85%+ using slow steaming when conditions favor it. Less mature options like bubble curtains under the hull or wind sails could add to the savings in the future.
Penciling Out The Economics
Lower battery costs combined with the benefits of electrification can reduce costs. An iron-air battery cycle might cost less than $100/MWh if we assume $20/kWh, 800 cycles, $40/MWh charging, and add $10/MWh for discounting and OPEX.
Fuel expenses can almost halve assuming 30%-50% better efficiency and wholesale electricity prices of $30-$40/MWh. Cargo capacity loss would also decrease with the efficiency improvement. Other benefits include reducing manning (~1/3 of the crew works on the engine), cutting maintenance, and increasing uptime.
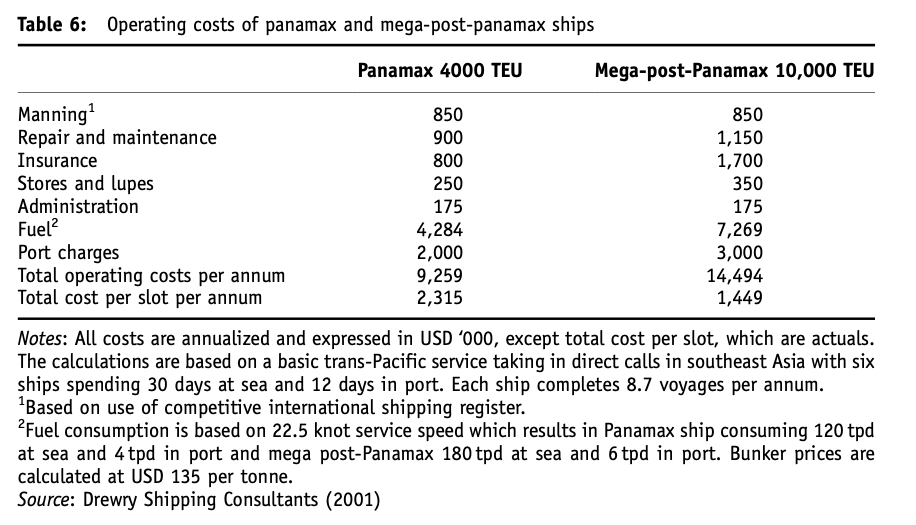
Fuel costs were $20/barrel when these numbers were taken! Source
The question becomes what number of battery swapping port calls maximizes profitability. More stops free up cargo space, provide more chances to load and unload paying cargo, and reduce battery leasing costs. The negatives are lost time, increased port charges, and risk of delays.
Ship CAPEX, the biggest expense behind fuel, should also fall. Electric motors, inverters, and power electronics will be cheaper than marine diesel engines. The batteries will likely be leased per journey, making them an operating cost like fuel. Complexity is being taken out of the ship because there will be fewer crew quarters, fewer ballast tanks, no fuel tanks, no fuel transfer equipment, no emissions abatement systems, and no giant engines. Any mass reduction is helpful, and designs might incorporate features like a deeper draft to increase mass capacity, limiting the impact of batteries on cargo capacity.
I've focused on container ships, but bulk carriers (hauling iron ore, grain, etc.) and crude tankers could also be electrified. They have blockier designs with deeper drafts to accommodate more mass in the same space. Container ships travel 18-24 knots because customers suffer while waiting on their expensive cargo. Bulk carriers and tankers cross the seas at 12-15 knots to minimize fuel costs. The number of batteries required to power them shrinks to more reasonable numbers. A Very Large Crude Carrier might only lose ~10% of its mass capacity (before any hull or propulsion efficiency improvements) to batteries in our cross-Atlantic, LFP battery case. Volume loss would be minimal.
Falling battery and wholesale electricity prices will make the economics even more compelling in the long term. Decreasing battery cost will come with incremental improvements in energy density because there will be extreme pressure to eliminate non-active mass and volume. As batteries become cheaper, it makes sense to keep extra batteries onshore and only charge with the least expensive off-peak power. Battery chargers can sell their power to the next ship, competing at $100/MWh, instead of waiting for rare price spikes in wholesale electricity markets.
Innovating Business Models
The defining shipping industry trends have been expanding trade and ever-larger ships to take advantage of economies of scale. Returns to scale are strong both in operating costs and capital costs. These new ships stretch existing infrastructure and led to congestion at ports. Electric ships can be competitive at smaller sizes due to CAPEX and OPEX reductions, but there will still be massive returns to scale. Several possible strategies jump out:
-
Access Small Ports
Smaller ships can access uncongested ports left behind by the growing size of cargo ships. Fleet Zero plans to use this business model with Southwest Airlines-like short hops between cities. They will give up significant performance to access these ports since smaller ships are typically less energy efficient.
-
More Point-to-Point Routes
More trading pairs will be feasible for non-stop service, reducing shipping times. These pairs will likely be <2000 miles apart.
-
Massive Offshore Shipping Hubs
Big ships, cramped ports, and schedule lumpiness conspire to lengthen shipping times and create costly delays. Expanding and modernizing ports is expensive and takes coordination between the government, unions, and port operators. The US has protectionist rules that make dredging expensive, and some places, like Africa, have few natural ports to expand.
An answer might be offshore superports designed to handle the largest ships. The facilities would act like Walmart distribution centers, with cargo quickly loaded onto smaller, electric feeder ships that deliver the goods at small ports close to customers. Having fewer routes with higher density makes organizing cargo for large ships simpler and reduces cargo dwell time in ports. Low-cost electric feeder ships enable regular deliveries to smaller ports. The overall concept could increase throughput while reducing shipping times.
The offshore ports can be cost-effective because they avoid dredging and can utilize technology like dynamic mooring to eliminate the need for breakwaters (this is easier for bulk cargo than containers, but should be possible).
The wide operating range and low cost of electric powertrains give ship operators opportunities to vary speed and ship size. We should see more point-to-point routes, but transformative concepts require more coordination and crossing many special interests.
Kicking Off Ship Electrification
Challenges with port infrastructure can slow adoption. One negative of charging off the ship is there needs to be space to store the batteries, electrical infrastructure to charge them, and transportation between the storage area and the docks. The logical place to start might be with back-and-forth shuttle routes that are ~1000 miles in length. The ship would only need to swap batteries at one port. The operators would get practice handling the batteries. Expansion of these bread routes could justify the charging infrastructure that allows more destinations.
Battery availability is another speed bump. Iron-air batteries are just hitting the market, and Form Energy's new factory will only produce enough cells for ten 10,000 TEU class ships each year. But they can scale to tens of terawatt-hours because iron, air, water, and hydroxide are abundant.
Ships are challenging for venture-backed startups because a small one might cost $20 million. A startup like Fleet Zero is starting with packaging commodity batteries in containers and converting used ships. Someone will still have to package iron-air batteries and account for some of their quirks, like needing a water supply. Then architects and engineers must design container ships, bulk carriers, and tankers that can use them. But a little momentum could drive rapid adoption. Ship lifetimes are only 10-15 years![2]
The Future is Electric
Battery electric powertrains keep trouncing alternative liquid fuels in replacing oil because they offer benefits and savings even at the early stages of adoption. Ships are no exception, and the back-of-the-envelope math suggests battery-electric ships could already be competitive with bunker fuel if they use low-cost battery chemistries and designs optimized for electrification. Electric ships can use any container outputting electricity so there may be many other propulsion options that join iron-air batteries. The industry could change rapidly once a company breaks the dam with a design that leverages electrification.
-
Aluminum-air batteries are another contender. They have higher specific energy (Wh/kg) than iron-air batteries and slightly better volumetric energy density. Their round-trip efficiency is lower at ~40%. They can also be very cheap, but only recharge "mechanically," where the active material is recycled. The actual battery can simpler because it has one electrode instead of two like rechargeable iron-air batteries, but handling is more intensive.
-
Many will want these ships produced in the US. Together Japan and South Korea produce more than half of the worlds ships. Japan has 70,000-80,000 shipyard workers and before COVID South Korea had 200,000. The US employs over 100,000 shipyard workers. A tiny portion of the current US workforce deployed at global productivity levels could make the US a top five ship building country. There is no need for industry expanding subsidies, just exposure to ruthless competition.
Why Battery Powered Cargo Ships are Compelling
2023 May 9 Twitter Substack See all postsShips need cheap batteries instead of high performance ones.
Battery-Powered Ship Basics
The Challenges
Most climate analysts consider cargo ships hard to decarbonize. I think this is for several reasons:
The popular battery chemistries have excellent power density to accelerate cars or regulate electricity grid frequency. They need constant use to recoup their high cost. Batteries that can discharge in a few hours are massive overkill when ships might prefer to go one week or more without charging.
People calculate how many batteries it takes to replace all the fuel cargo ships carry or assume an extreme trip length.
It would take too long to charge or fast charging a ship dockside would have a horrific power draw.
Ships are great at carrying bulky and heavy stuff with minimal cost and energy usage. We need a battery chemistry that leans into that and sacrifices performance to reduce cost. Electrification also requires a different business model for charging the batteries.
Checking the Math
Let's examine powering a 10,000 TEU container ship from New York to Rotterdam with the cheapest volume battery chemistry we have, lithium iron phosphate (LFP). At the max continuous speed of 22 knots, power usage is ~40 MW. The trip distance is 3800 miles, so we need ~150 hours of power or 6 GWh. These ships carry ~2 million gallons of fuel, which equates to ~7.5 million liters. The latest CATL Qilin LFP packs contain 290 Wh/l. We can fit nearly 2.2 GWh just in our fuel storage space. Two-stroke marine diesel engines are massive, and we can get another ~0.5 GWh from reducing engine room space and ballast. The last 3.6 GWh can fit in less than 450 TEUs. So we can cross oceans losing only 4.5% of cargo space while gaining the benefits of electrification. The mass performance is not as good, with the batteries using 25% of the cargo mass after netting out fuel and engines. Ships carrying lighter containers would see little cargo penalty, but those carrying heavier goods would.
They get way bigger than this! Source
The startup Fleet Zero has a solution for the charging problem - containerize the batteries, charge them nearby the port, and load them like regular cargo. Ships carry so much fuel today because few fuel sales points offer the required scale, quality, and cost. Filling up at the best places and using large fuel tanks is the way to minimize cost. Recharging at each port will be the lowest cost strategy if batteries and electricity are cheaper than fuel, even if there is variation in prices between ports.
The issue with using LFP batteries is cost. 6 GWh of LFP batteries would cost over $600 million. The cost per cycle would be $110/MWh plus charging costs that could be anywhere from $30/MWh to $100/MWh. Heavy fuel oil at $80/barrel in a 45% efficient engine equates to ~$110/MWh. Business models like Fleet Zero assume multiple stops on routes (which cargo ships commonly do, anyway) and slower speeds. Ships carry fewer batteries on each leg, and the system requires fewer batteries. Cost per cycle drops to reasonable levels while cargo penalties decrease. But it would make adoption easier if cheaper batteries allowed ships to carry more batteries or increased their savings.
These numbers contrast with calculations from analysts like Vaclav Smil because he assumes a 30+ day non-stop trip from Asia to Europe. But shipping companies are in the business of making money, not non-stop voyages. They will stop a few times to swap batteries if it increases profitability.
Iron-Air Batteries to the Rescue?
Iron-Air Fundamentals
Iron-air batteries charge by turning rust into iron, releasing oxygen while absorbing electrons. They do the reverse to provide power. Their theoretical energy density is higher than today's batteries because they can get oxygen from the air instead of carrying it around in another material. The systems and conditions needed to make the batteries work lower their energy density close to mass market batteries, though that will likely improve with further iteration. A sometimes important feature for ships is that iron-air battery volumetric energy density (Wh/l) is much better than its specific energy (Wh/kg), helping vessels that might be space limited.
The battery models coming to market discharge in 100-150 hours, meaning ships will carry enough batteries for at least 4-6 days of travel.
Researchers studied iron-air batteries for cars in the 1970s. Getting them to work at high power densities and with enough cycles was challenging. Entrepreneurs have recently resurrected the technology for low-power applications like multi-day electricity storage. Research on the critical air-breathing cathode restarted in the mid-2000s, and the maturation of that technology led to the startup Form Energy breaking ground on a 50 gigawatt-hour-per-year factory in West Virginia in early 2023.
Other battery chemistries might fit better, but the iron-air chemistry is the only one with a gigawatt scale factory under construction.[1]
The Cargo Ship Use Case
Iron-air chemistry's best features for ships are its low cost, acceptable volumetric energy density, and low fire risk. The current manufacturing cost is likely between $20/kWh and $50/kWh. Form Energy's goal is $20/kWh, and the active material is only $6/kWh. The battery industry has been ruthless at eliminating non-active material from other chemistries. Prices might creep toward $10/kWh at scale. Energy density could be anywhere from 200 Wh/l to 1000 Wh/l based on historical research results. Iron-air batteries can't undergo thermal runaway like lithium-ion batteries, an advantage for ships where fire is a concern.
The negatives of iron-air batteries are low power density, limited cycle life, and poor charge efficiency. Power density isn't a big deal to ships because they want to use energy steadily rather than expending it in short bursts. Lower cycle life is manageable because batteries meant to discharge for days use fewer cycles. If a battery only does 40 cycles per year, 800 is a twenty-year supply! Thousands of uses are overkill. Iron-air batteries could also be amenable to inexpensive "refurbishment" rather than wholesale replacement. Charge efficiency is poor compared to lithium-ion batteries - only 60%. But losing some cheaper electricity is acceptable when competing with expensive liquid fuels.
Improving Ship Efficiency
Engineers almost always find ways to improve efficiency when designing electric vehicles. Better efficiency can improve range or reduce battery pack size besides cutting energy costs. Ships lose most energy through waste heat, propeller loss, and hull friction. Electric motors are much more efficient than marine engines, so the focus is on propellers and hull friction.
Hulls, propellers, and engines bleed energy. Source
There are many low-risk opportunities:
More Efficient Hull Forms
Optimized hull designs can be up to 20% more efficient than traditional ones. A 2016 report cites barriers to adoption as more upfront design time and coordination with shipyards. There will be more design and coordination effort when designing early battery-electric ships, so a better hull form should be a relatively easy bolt-on.
Better Hull Coatings
Anti-fouling coatings can reduce fuel usage by ~3% and will likely be more valuable to a battery electric ship than an oil-fueled one because of range extension.
Optimal Propeller Design and Conditioning
Ships can reduce fuel usage by 15%-20% by using more efficient propellers and improving the water flow conditions around them.
Large cargo ships almost all use giant two-stroke marine engines because they are efficient and reliable. Another advantage of two-stroke engines is that their slower-than-normal speed means they can directly drive propellers without expensive and complicated gears. That speed and location are not optimal for propeller efficiency, though.
Electric ships can use larger propellers with lower RPMs that are more efficient. They can also place the propellers further outside the wake using propulsion pods because electric motors are tiny compared to marine engines. Many cruise ships already use these because diesel-electric powertrains better match their requirements than direct-drive powertrains.
Fins and other devices can smooth the flow around the pods, further improving propeller efficiency.
Wider Efficiency Curves
The flexibility of electric powertrains can provide another 5%-10% reduction in fuel usage. Engines have a very narrow range where they operate at peak efficiency. In the real world, they rarely run in optimal conditions. Electric motors have good efficiency across a wide range of speeds.
Slow Steaming
Ships usually slow down when fuel costs are high because reducing speed can cut fuel consumption dramatically. A problem for ships with marine diesel engines is that engine efficiency drops precipitously at lower RPMs, resulting in diminishing returns for slow steaming. Electric motors don't share this issue, so they get the full benefits of slower travel. An electric ship will use ~1/8th of the power and ~1/4th of the energy to complete a trip if it halves its speed. Ship owners gain the ability to load up the batteries and blaze ahead if spot freight prices are high, or they can slow down to extend range and reduce costs if necessary. It is challenging to have both options with traditional cargo ships.
Reducing speed has diminishing returns for fuel consumption. Source
But only because of decreasing efficiency, delivered power still falls dramatically. Source
Other Operational Improvements
Accounting for weather in navigation plans, adjusting speed to allow for on-time arrivals, and optimizing trim and draft can cut fuel usage by ~8%. These will be more valuable to battery electric ships and might be easier to implement with electric powertrains.
Battery requirements should decrease by 25%-50% without losing any performance. There is an opportunity to reduce energy usage by 85%+ using slow steaming when conditions favor it. Less mature options like bubble curtains under the hull or wind sails could add to the savings in the future.
Penciling Out The Economics
Lower battery costs combined with the benefits of electrification can reduce costs. An iron-air battery cycle might cost less than $100/MWh if we assume $20/kWh, 800 cycles, $40/MWh charging, and add $10/MWh for discounting and OPEX.
Fuel expenses can almost halve assuming 30%-50% better efficiency and wholesale electricity prices of $30-$40/MWh. Cargo capacity loss would also decrease with the efficiency improvement. Other benefits include reducing manning (~1/3 of the crew works on the engine), cutting maintenance, and increasing uptime.
Fuel costs were $20/barrel when these numbers were taken! Source
The question becomes what number of battery swapping port calls maximizes profitability. More stops free up cargo space, provide more chances to load and unload paying cargo, and reduce battery leasing costs. The negatives are lost time, increased port charges, and risk of delays.
Ship CAPEX, the biggest expense behind fuel, should also fall. Electric motors, inverters, and power electronics will be cheaper than marine diesel engines. The batteries will likely be leased per journey, making them an operating cost like fuel. Complexity is being taken out of the ship because there will be fewer crew quarters, fewer ballast tanks, no fuel tanks, no fuel transfer equipment, no emissions abatement systems, and no giant engines. Any mass reduction is helpful, and designs might incorporate features like a deeper draft to increase mass capacity, limiting the impact of batteries on cargo capacity.
I've focused on container ships, but bulk carriers (hauling iron ore, grain, etc.) and crude tankers could also be electrified. They have blockier designs with deeper drafts to accommodate more mass in the same space. Container ships travel 18-24 knots because customers suffer while waiting on their expensive cargo. Bulk carriers and tankers cross the seas at 12-15 knots to minimize fuel costs. The number of batteries required to power them shrinks to more reasonable numbers. A Very Large Crude Carrier might only lose ~10% of its mass capacity (before any hull or propulsion efficiency improvements) to batteries in our cross-Atlantic, LFP battery case. Volume loss would be minimal.
Falling battery and wholesale electricity prices will make the economics even more compelling in the long term. Decreasing battery cost will come with incremental improvements in energy density because there will be extreme pressure to eliminate non-active mass and volume. As batteries become cheaper, it makes sense to keep extra batteries onshore and only charge with the least expensive off-peak power. Battery chargers can sell their power to the next ship, competing at $100/MWh, instead of waiting for rare price spikes in wholesale electricity markets.
Innovating Business Models
The defining shipping industry trends have been expanding trade and ever-larger ships to take advantage of economies of scale. Returns to scale are strong both in operating costs and capital costs. These new ships stretch existing infrastructure and led to congestion at ports. Electric ships can be competitive at smaller sizes due to CAPEX and OPEX reductions, but there will still be massive returns to scale. Several possible strategies jump out:
Access Small Ports
Smaller ships can access uncongested ports left behind by the growing size of cargo ships. Fleet Zero plans to use this business model with Southwest Airlines-like short hops between cities. They will give up significant performance to access these ports since smaller ships are typically less energy efficient.
More Point-to-Point Routes
More trading pairs will be feasible for non-stop service, reducing shipping times. These pairs will likely be <2000 miles apart.
Massive Offshore Shipping Hubs
Big ships, cramped ports, and schedule lumpiness conspire to lengthen shipping times and create costly delays. Expanding and modernizing ports is expensive and takes coordination between the government, unions, and port operators. The US has protectionist rules that make dredging expensive, and some places, like Africa, have few natural ports to expand.
An answer might be offshore superports designed to handle the largest ships. The facilities would act like Walmart distribution centers, with cargo quickly loaded onto smaller, electric feeder ships that deliver the goods at small ports close to customers. Having fewer routes with higher density makes organizing cargo for large ships simpler and reduces cargo dwell time in ports. Low-cost electric feeder ships enable regular deliveries to smaller ports. The overall concept could increase throughput while reducing shipping times.
The offshore ports can be cost-effective because they avoid dredging and can utilize technology like dynamic mooring to eliminate the need for breakwaters (this is easier for bulk cargo than containers, but should be possible).
The wide operating range and low cost of electric powertrains give ship operators opportunities to vary speed and ship size. We should see more point-to-point routes, but transformative concepts require more coordination and crossing many special interests.
Kicking Off Ship Electrification
Challenges with port infrastructure can slow adoption. One negative of charging off the ship is there needs to be space to store the batteries, electrical infrastructure to charge them, and transportation between the storage area and the docks. The logical place to start might be with back-and-forth shuttle routes that are ~1000 miles in length. The ship would only need to swap batteries at one port. The operators would get practice handling the batteries. Expansion of these bread routes could justify the charging infrastructure that allows more destinations.
Battery availability is another speed bump. Iron-air batteries are just hitting the market, and Form Energy's new factory will only produce enough cells for ten 10,000 TEU class ships each year. But they can scale to tens of terawatt-hours because iron, air, water, and hydroxide are abundant.
Ships are challenging for venture-backed startups because a small one might cost $20 million. A startup like Fleet Zero is starting with packaging commodity batteries in containers and converting used ships. Someone will still have to package iron-air batteries and account for some of their quirks, like needing a water supply. Then architects and engineers must design container ships, bulk carriers, and tankers that can use them. But a little momentum could drive rapid adoption. Ship lifetimes are only 10-15 years![2]
The Future is Electric
Battery electric powertrains keep trouncing alternative liquid fuels in replacing oil because they offer benefits and savings even at the early stages of adoption. Ships are no exception, and the back-of-the-envelope math suggests battery-electric ships could already be competitive with bunker fuel if they use low-cost battery chemistries and designs optimized for electrification. Electric ships can use any container outputting electricity so there may be many other propulsion options that join iron-air batteries. The industry could change rapidly once a company breaks the dam with a design that leverages electrification.
Aluminum-air batteries are another contender. They have higher specific energy (Wh/kg) than iron-air batteries and slightly better volumetric energy density. Their round-trip efficiency is lower at ~40%. They can also be very cheap, but only recharge "mechanically," where the active material is recycled. The actual battery can simpler because it has one electrode instead of two like rechargeable iron-air batteries, but handling is more intensive.
Many will want these ships produced in the US. Together Japan and South Korea produce more than half of the worlds ships. Japan has 70,000-80,000 shipyard workers and before COVID South Korea had 200,000. The US employs over 100,000 shipyard workers. A tiny portion of the current US workforce deployed at global productivity levels could make the US a top five ship building country. There is no need for industry expanding subsidies, just exposure to ruthless competition.